ネジ山に発生した打痕
打痕は様々な場所に発生しますが、ネジ山などの複雑な凹凸がある場所に発生するダコンは 滑らかな面に発生する打痕と比較して検出が困難とされています。単純な二値化や画像比較では、複雑な凹凸やギラつきに対応できないためです。
AI(ディープラーニング)はパターンやテクスチャを見分けることができるため、このようなダコンも凹凸やギラつきの影響を受けずに検出することができます。
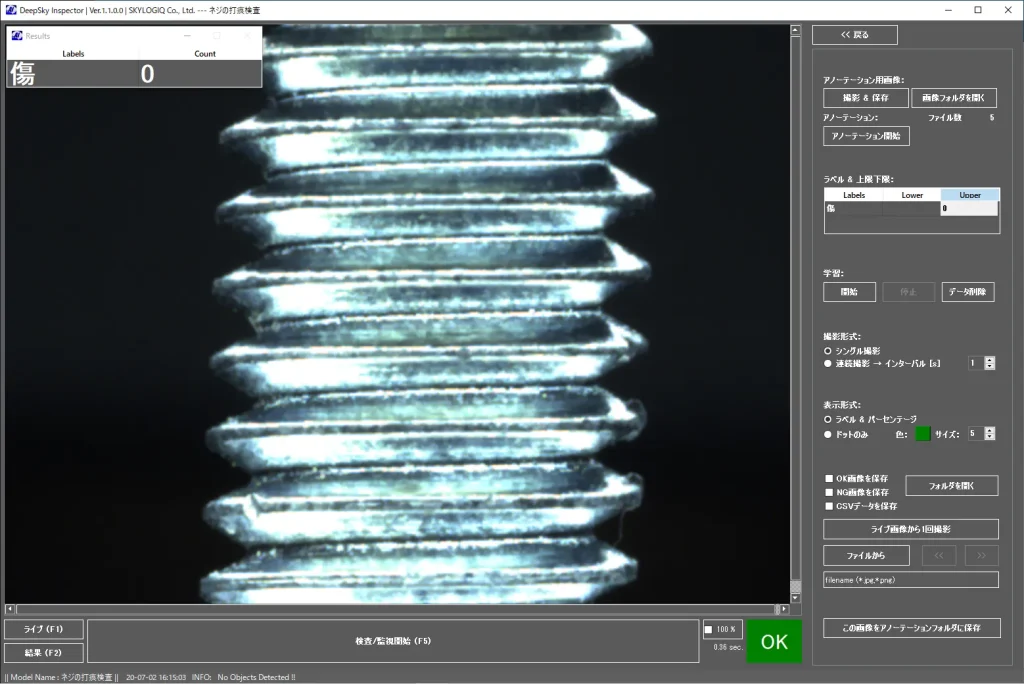
ダコンのない状態。ギラつきがかなり目立っていますが正しく判定されています。
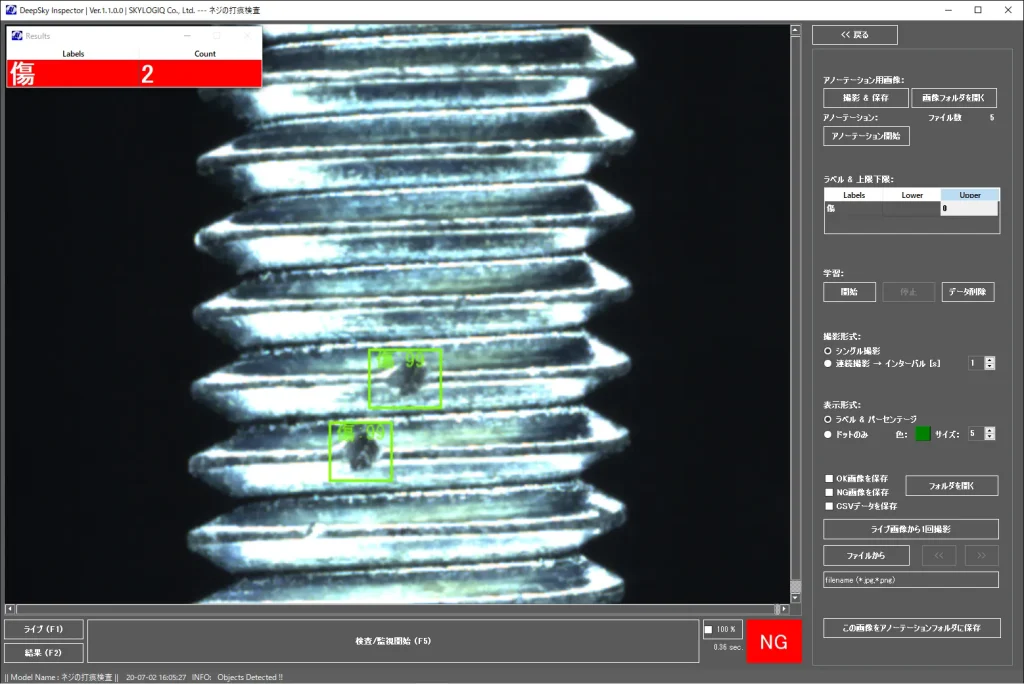
小さなダコンが発生している状態(NG)。ダコンだけをピンポイントで検出しています。
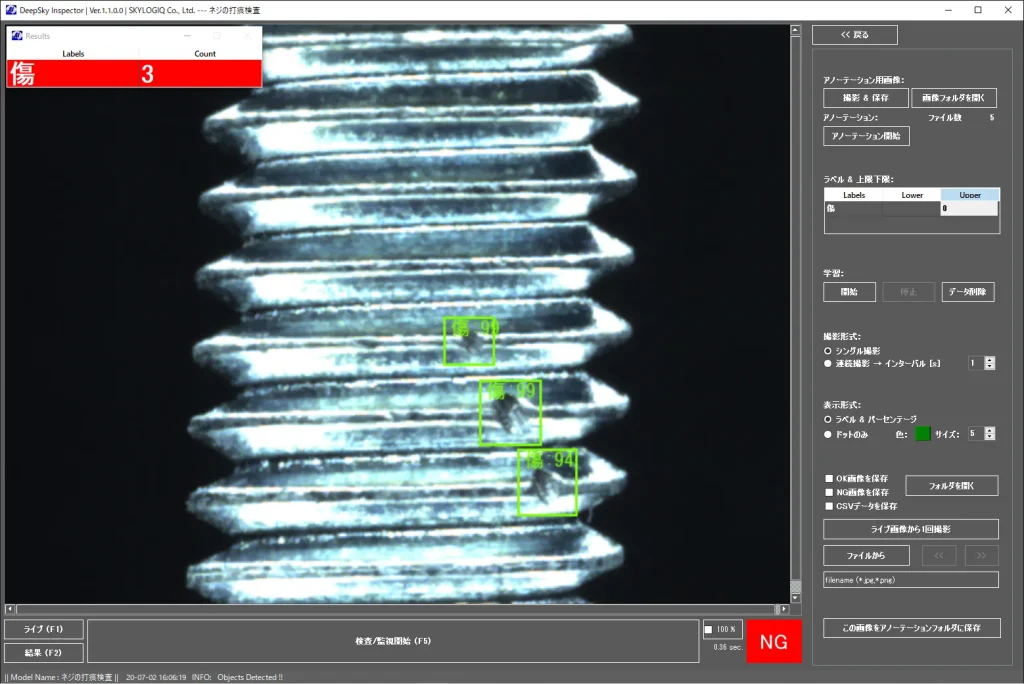
角度が変わっても正しく検出しています。
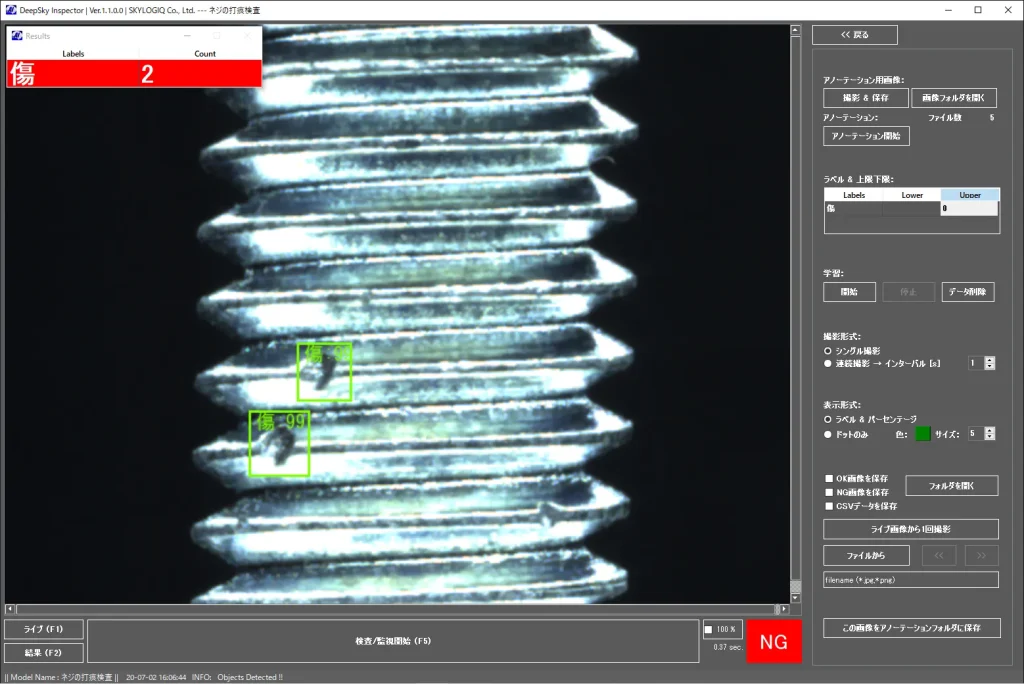
さらに小さなダコンも検出しています。
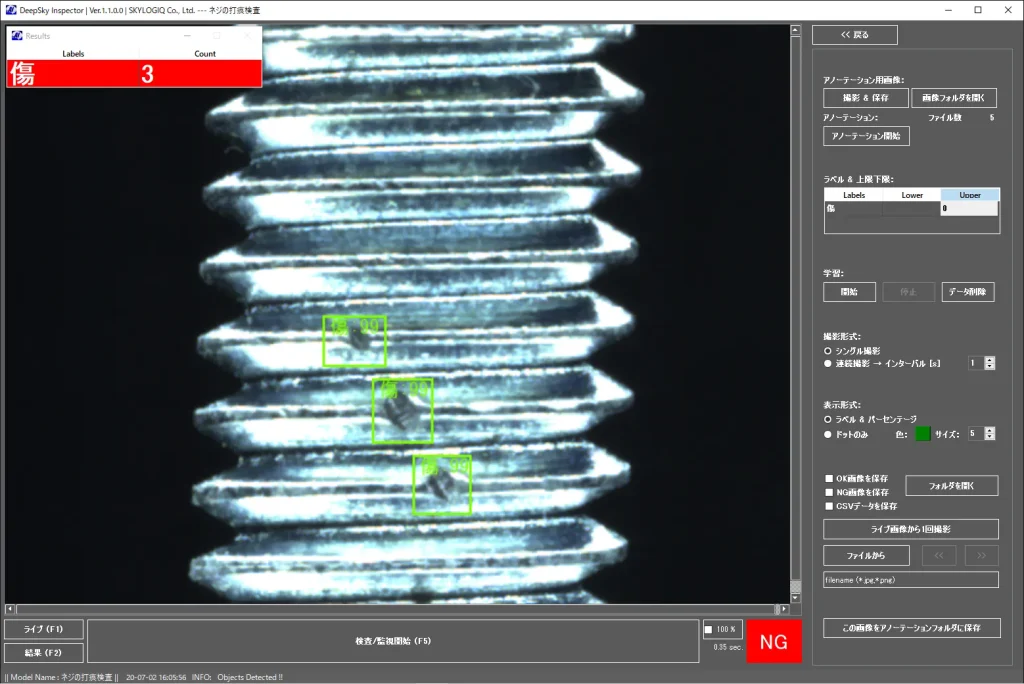
超高画素(3600万画素)での微小欠陥検出
超高画素一眼レフカメラを使い、300mm程度の広い視野を一度に撮影して微小な欠陥(0.2mm程度)を検出しています。FXCaptureを使用しています。マスター画像との比較ではなく、欠陥そのものが持つ画像的な特徴を捉えて検出する方式のため、別のパターンでも(またはパターンが変形しても)欠陥を検出することができます。
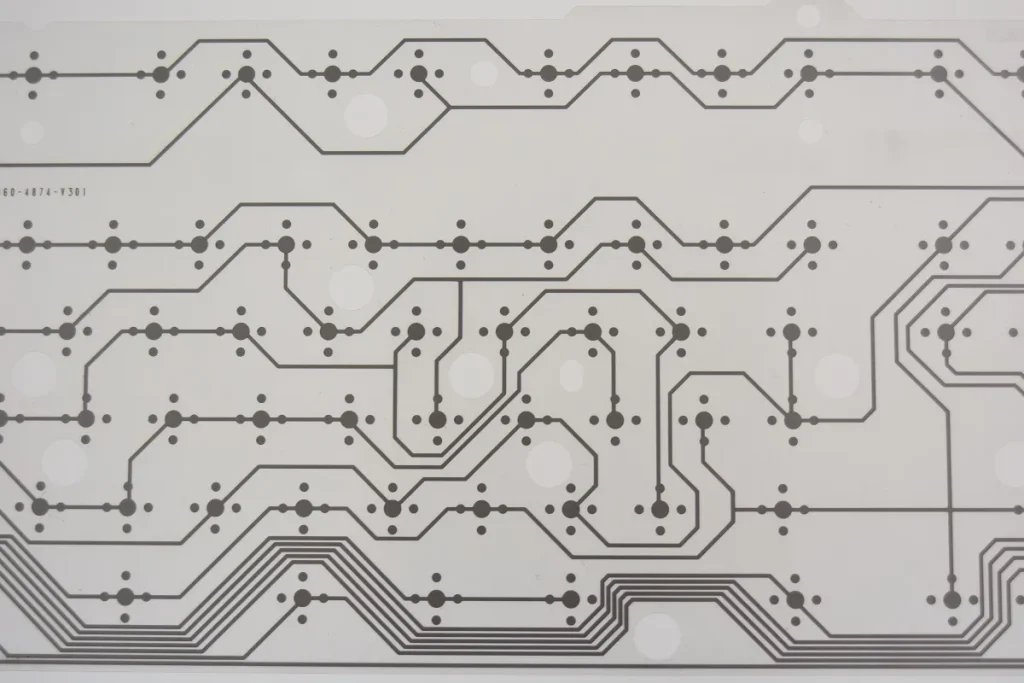
全体視野です。画面全体にパターンが印刷されています。
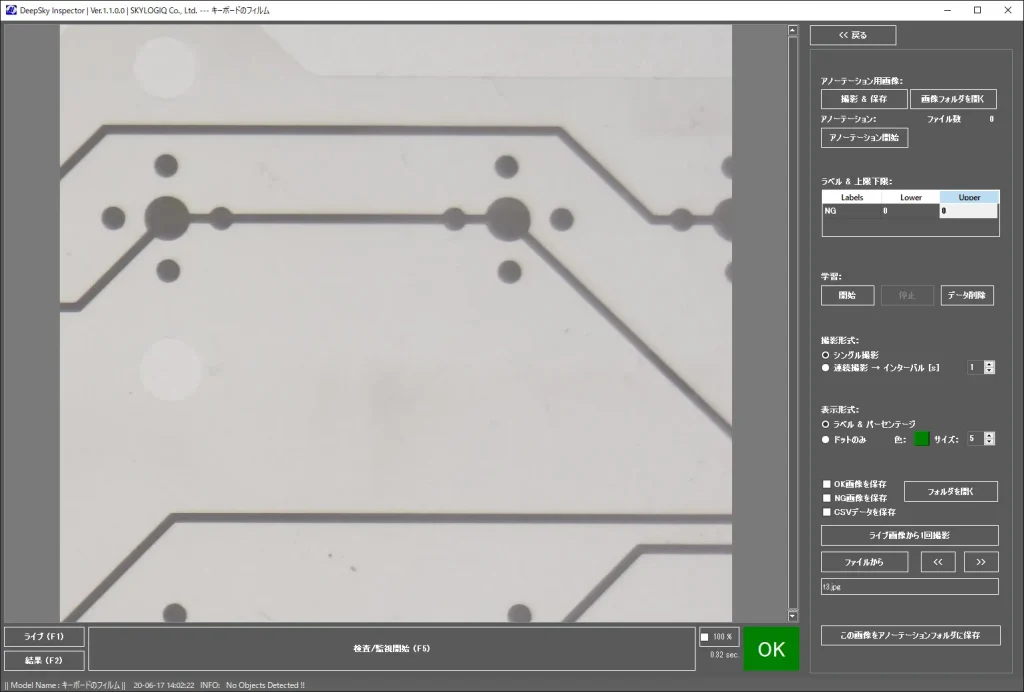
OKの状態。欠陥がありません。
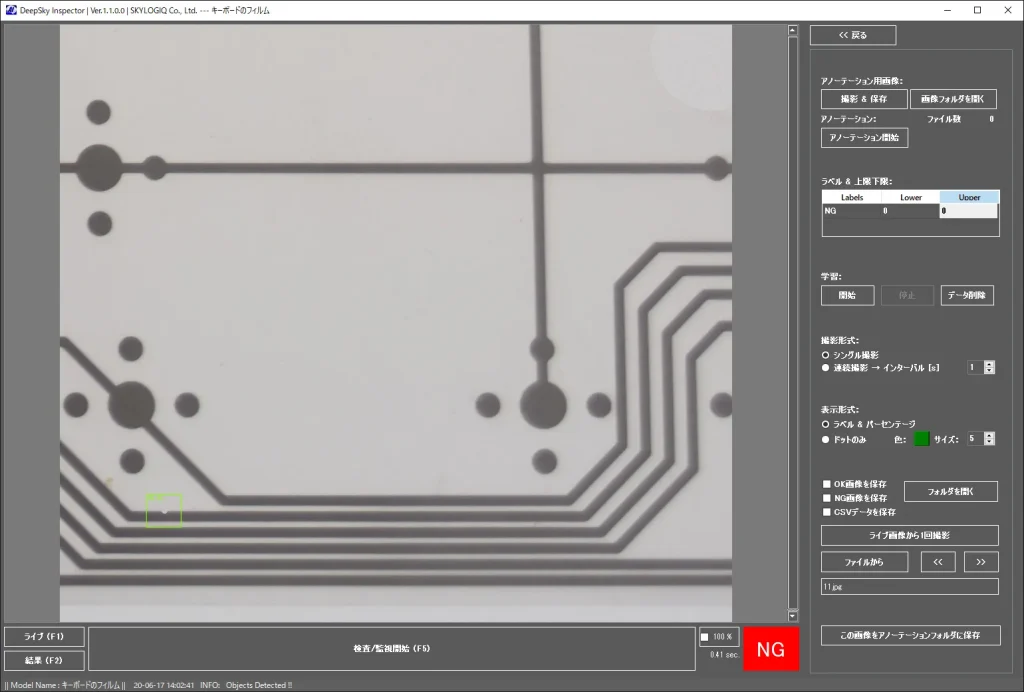
左下付近に微小なパターンの欠けがあります。
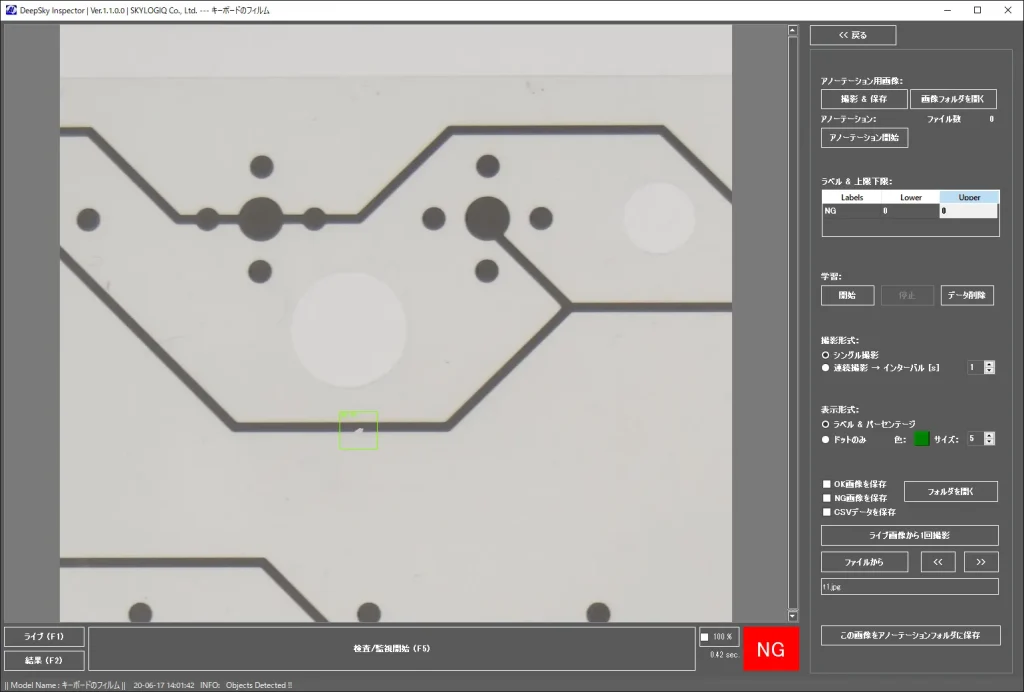
中央付近に微小なパターンの欠けがあります。
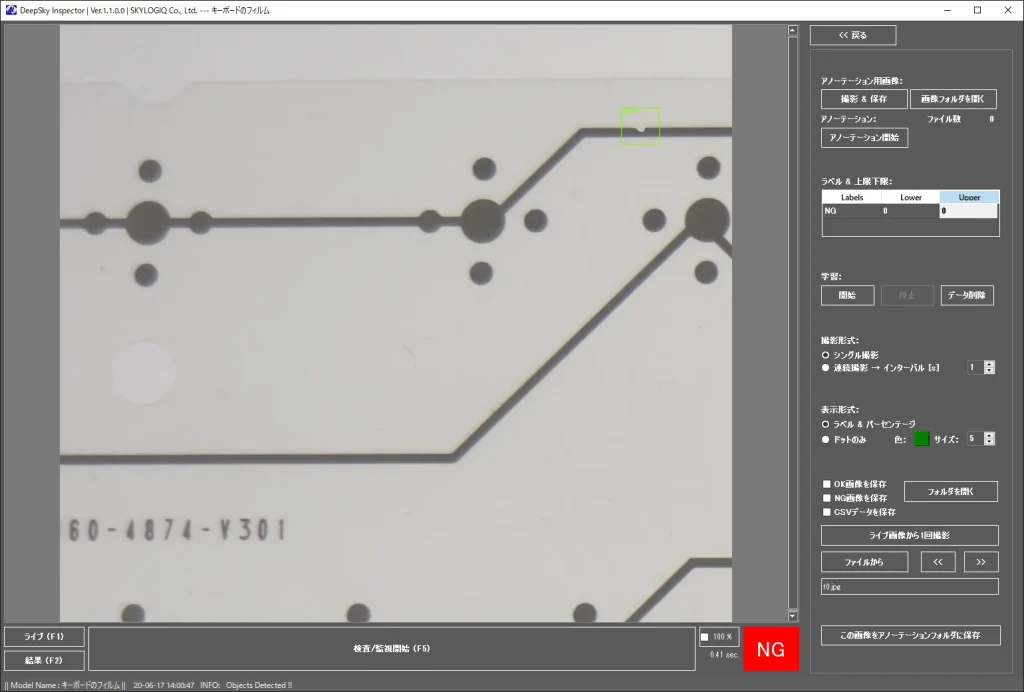
右上付近に微小なパターンの欠けがあります。
ハンダ無しとハンダ少の検出
電子基板上のハンダの状態を確認しています。ハンダの量によって判定を分けています。(画像クリックで拡大)
同軸落射照明を使用しています。
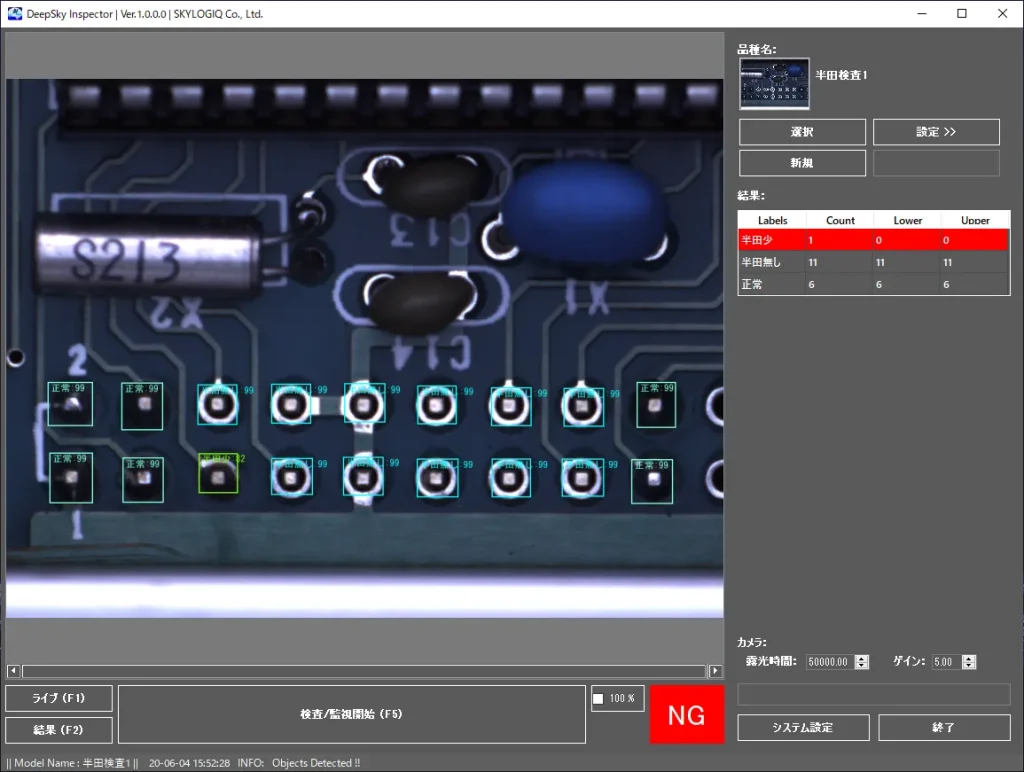
ハンダ無し、ハンダ少、正常の3種類に分けて判別しています。
金属エッチングと回路パターン印刷
エッチングのピンホールや欠け、クワレ
金属エッチングでは、気泡によってマスク印刷に穴があいていたりチリで印刷が浮いたりするとその部分がピンホールや欠けなどの欠陥になります。
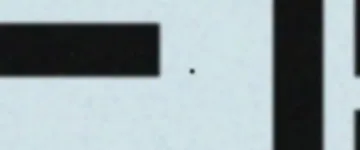
ピンホール
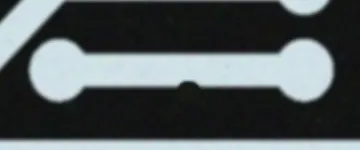
カケ
回路パターン印刷のツノ、ニジミ、フクレ
ガラスやセラミック、樹脂に印刷される回路パターンでは版元に不良があるとツノ、バリ、ニジミなどの不具合が発生し、早期に修正しないと不良を大量に発生させることになります。
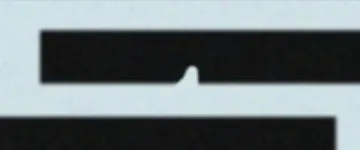
ツノ・バリ
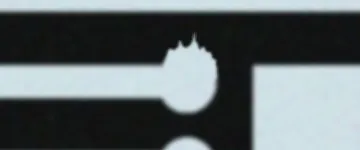
滲み
物体認識により欠陥を分類して検出
DeepSkyはこれらの欠陥を分類して検出することができます。またそれぞれの欠陥の数や座標も得ることができます。実際の運用では目視検査の補助としてDeepSkyで連続検査を実行しつつ、手でゆっくり動かして目視で検査する方法や X-Yステージを使って完全自動化する方法でご使用頂いています。
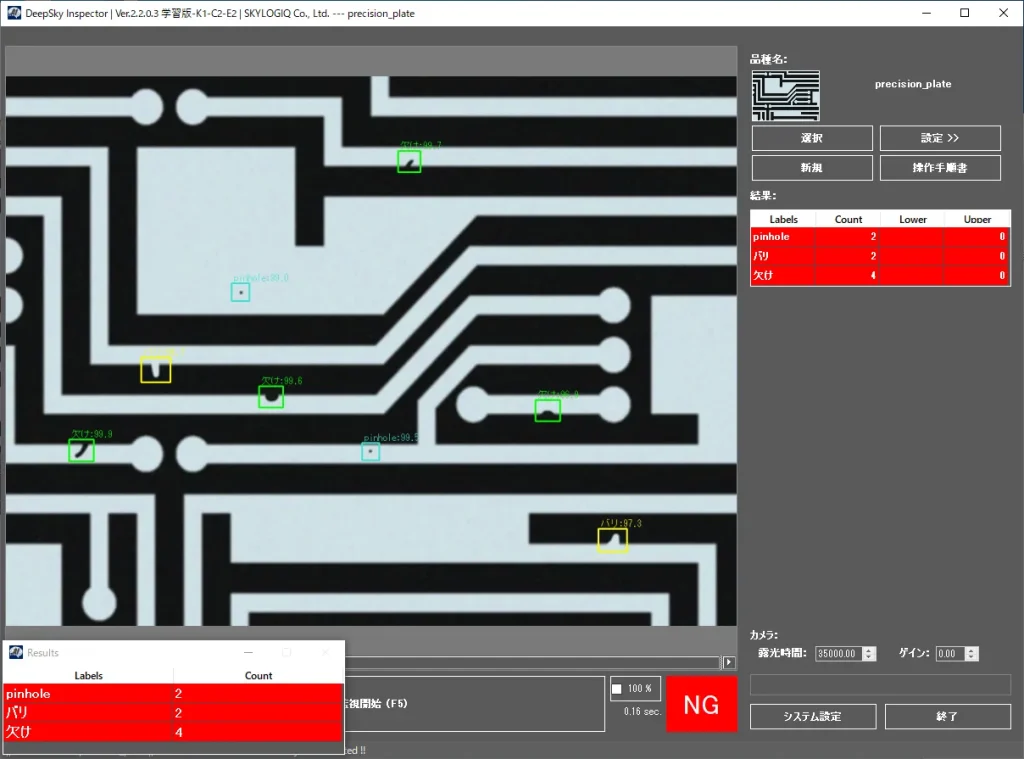
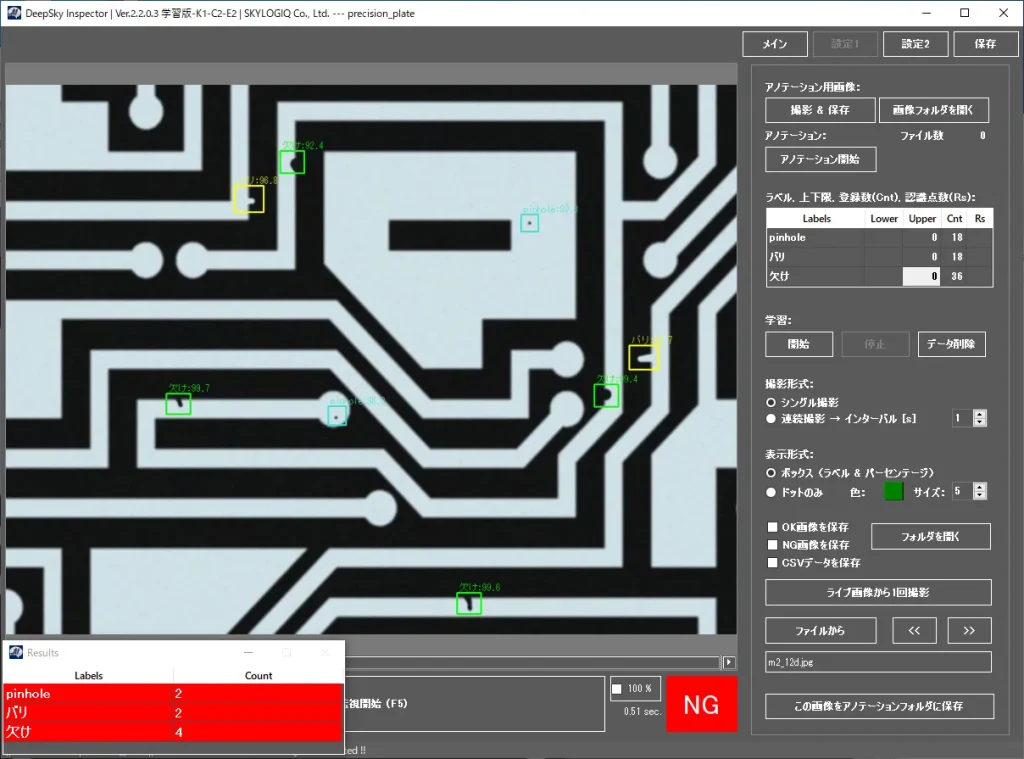
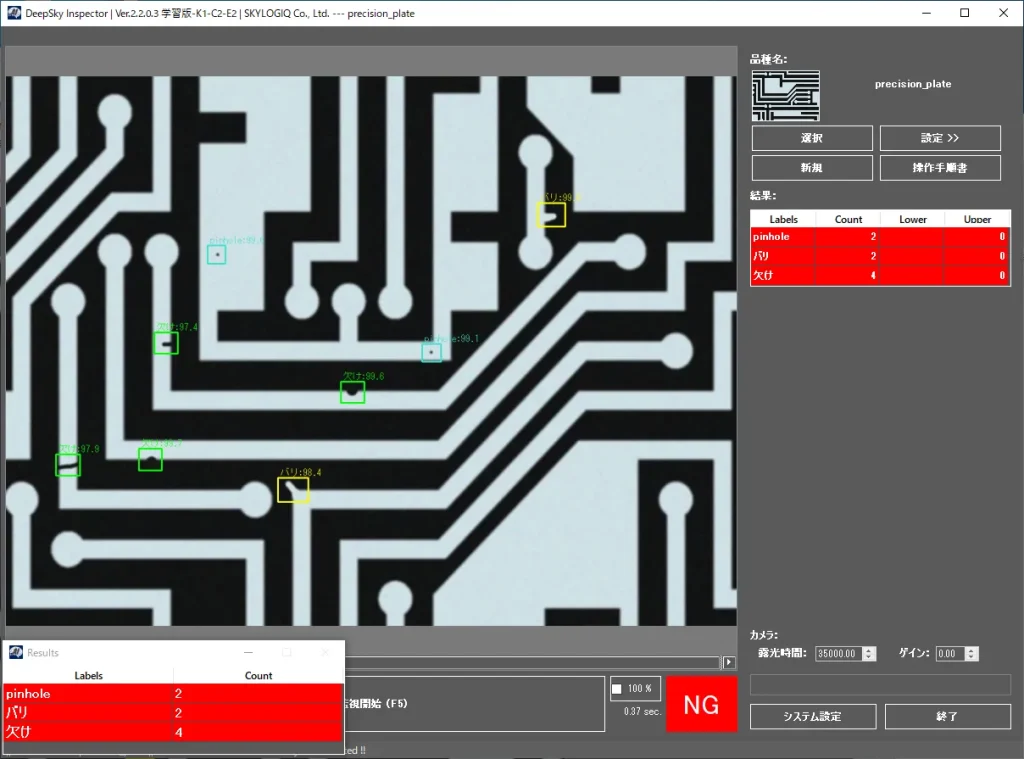
布製品の汚れやほつれ
学習させた異常箇所を検出し、NGと判定しています。(画像クリックで拡大表示)
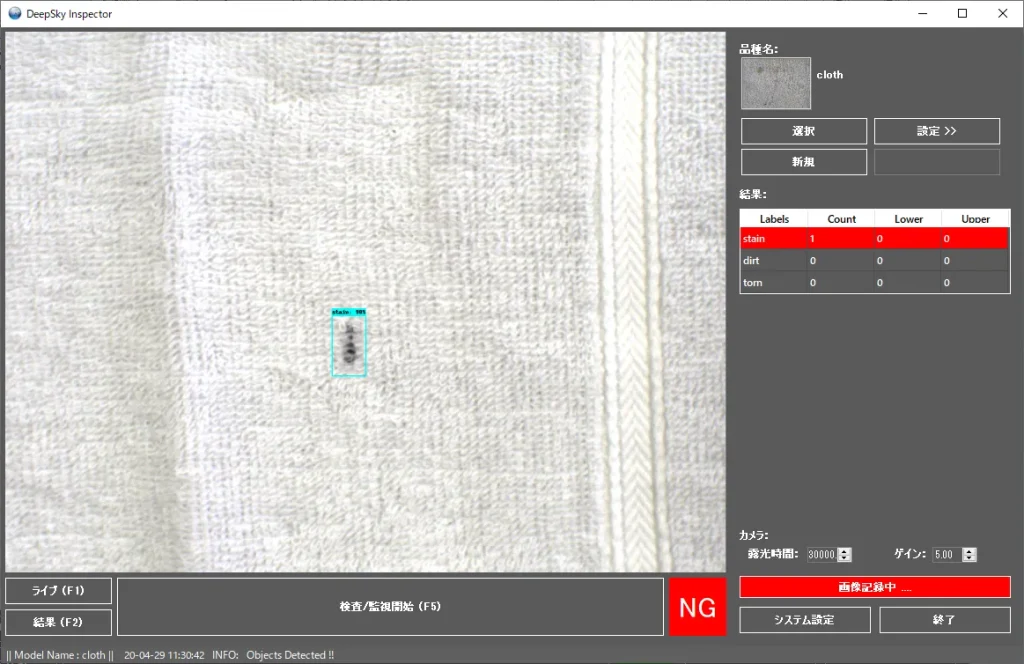
黒い汚れを検出し、NGと判定しています。
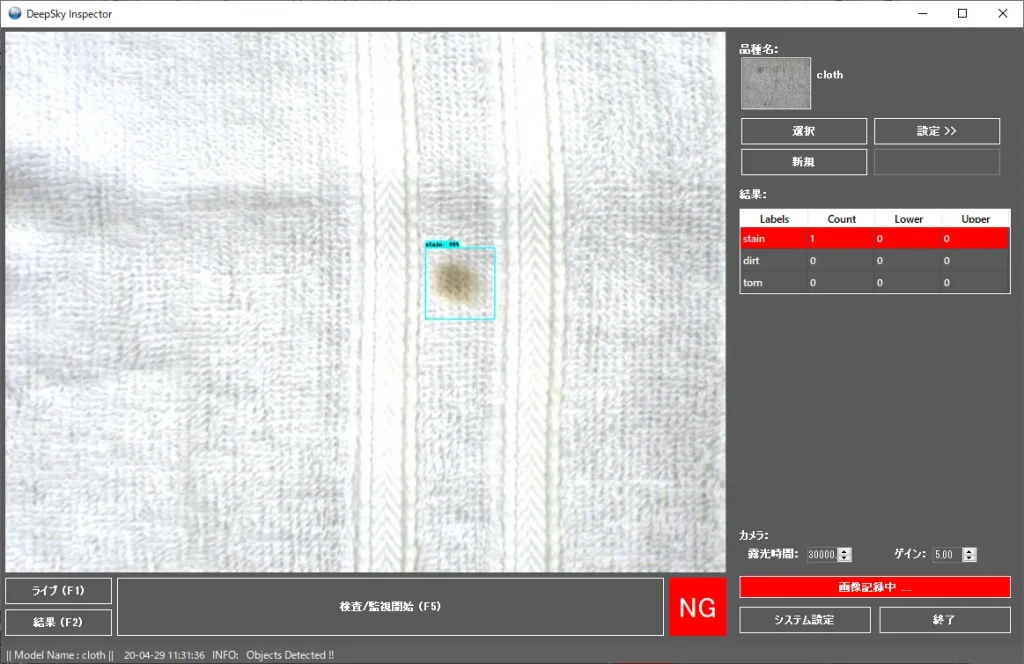
茶色い汚れを検出し、NGと判定しています。
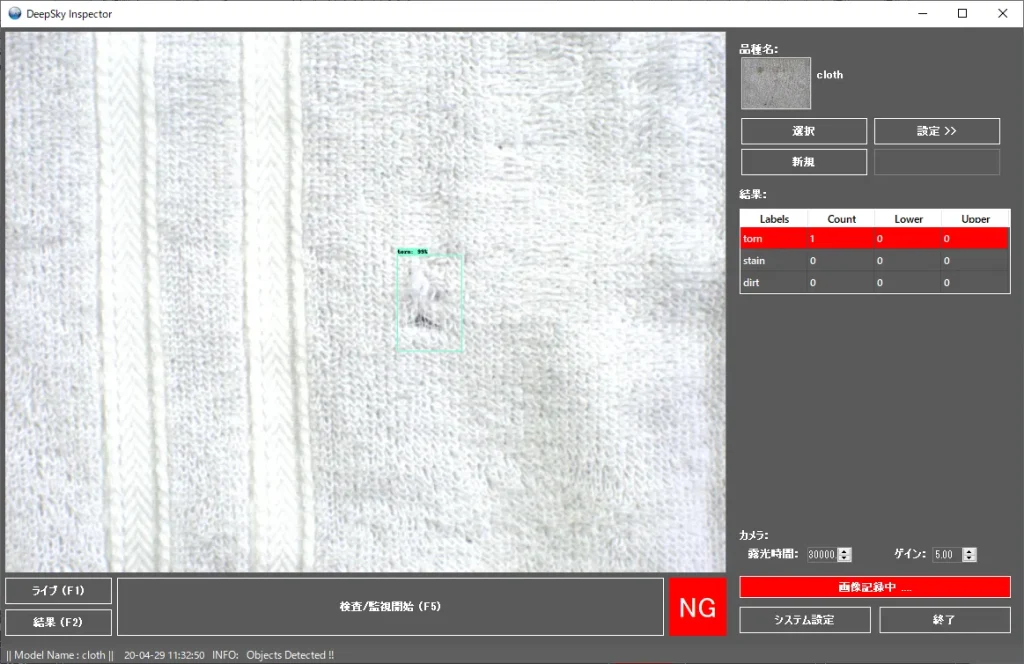
ほつれた部分を検出し、NGと判定しています。
発泡スチロールの欠陥
発泡スチロールのえぐれや黒点、汚れを検出して不合格と判定しています。(画像クリックで拡大表示)
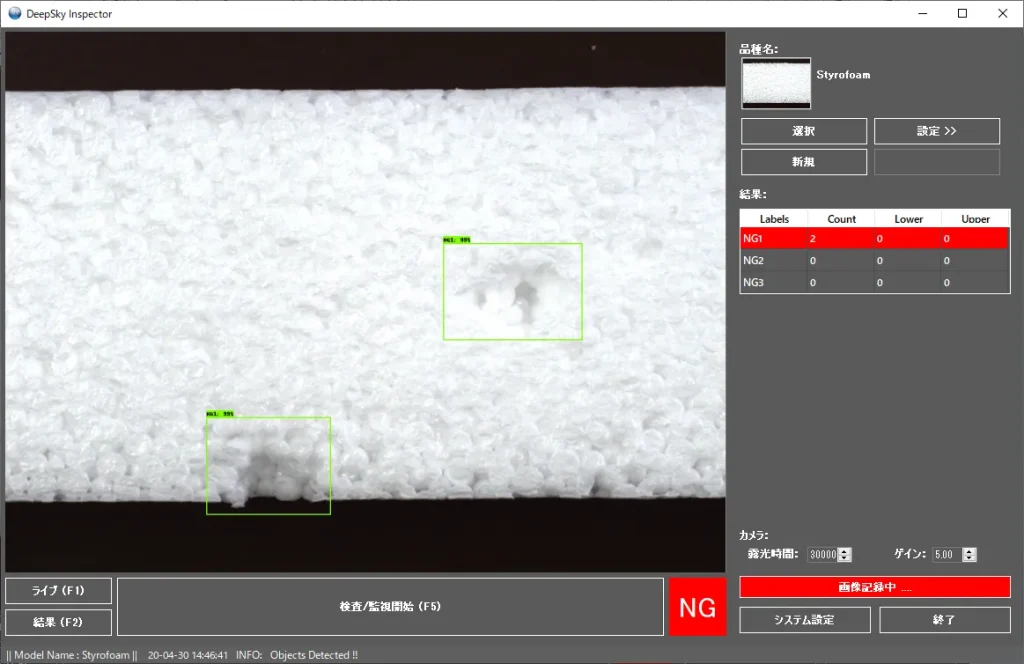
えぐれた部分を欠陥として検出し、NGと判定しています。
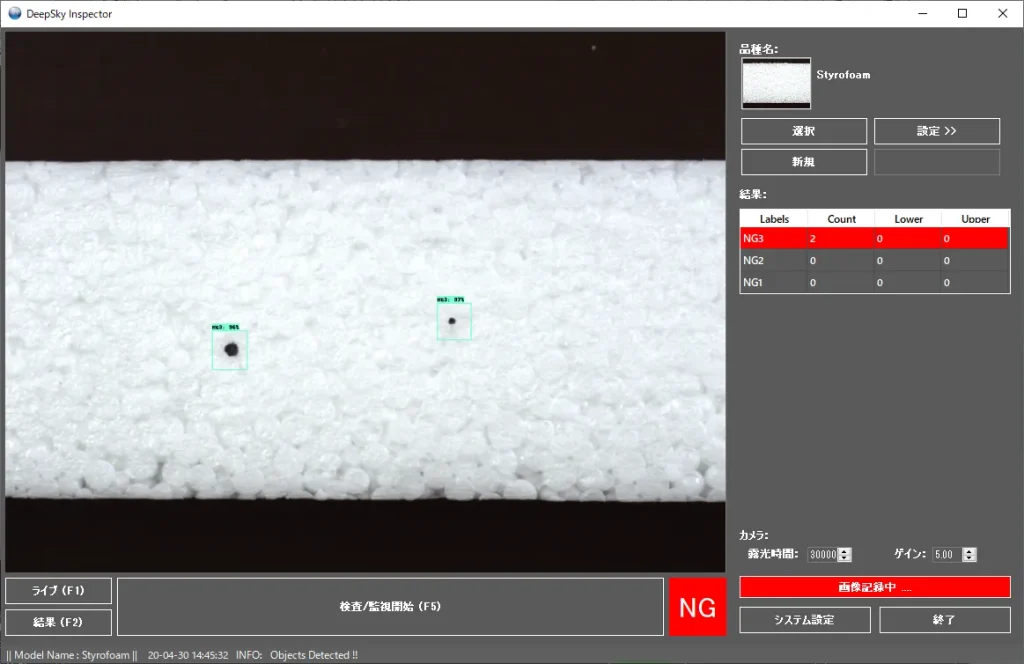
黒点を欠陥として検出し、NGと判定しています。
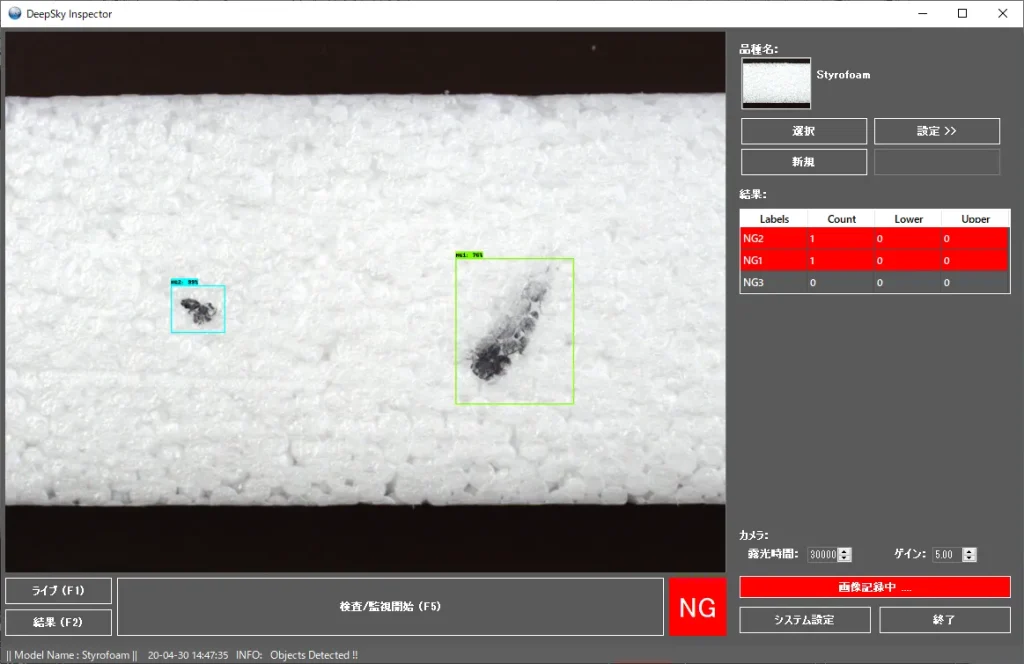
汚れた部分を欠陥として検出し、NGと判定しています。
シボ面の荒れ
シボ加工された表面など、テクスチャーを持つ表面では二値化などによる欠陥の発見は困難です。ディープラーニングはテクスチャーの異常を検出する用途に強みを発揮します。(クリックで画像拡大)
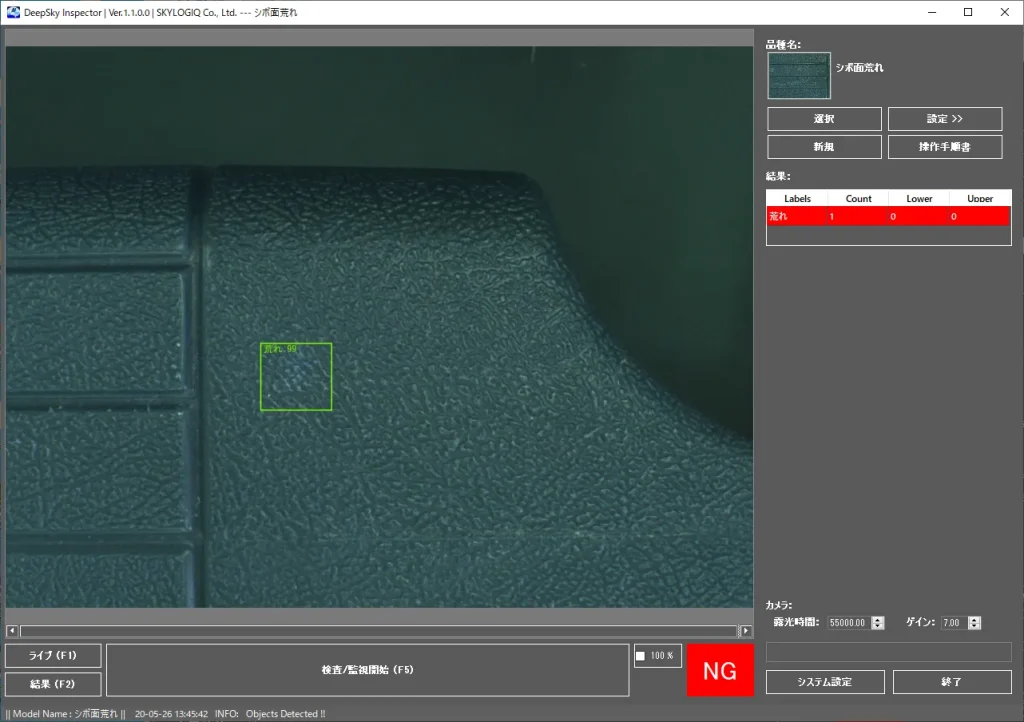
シボ面の軽微な荒れ
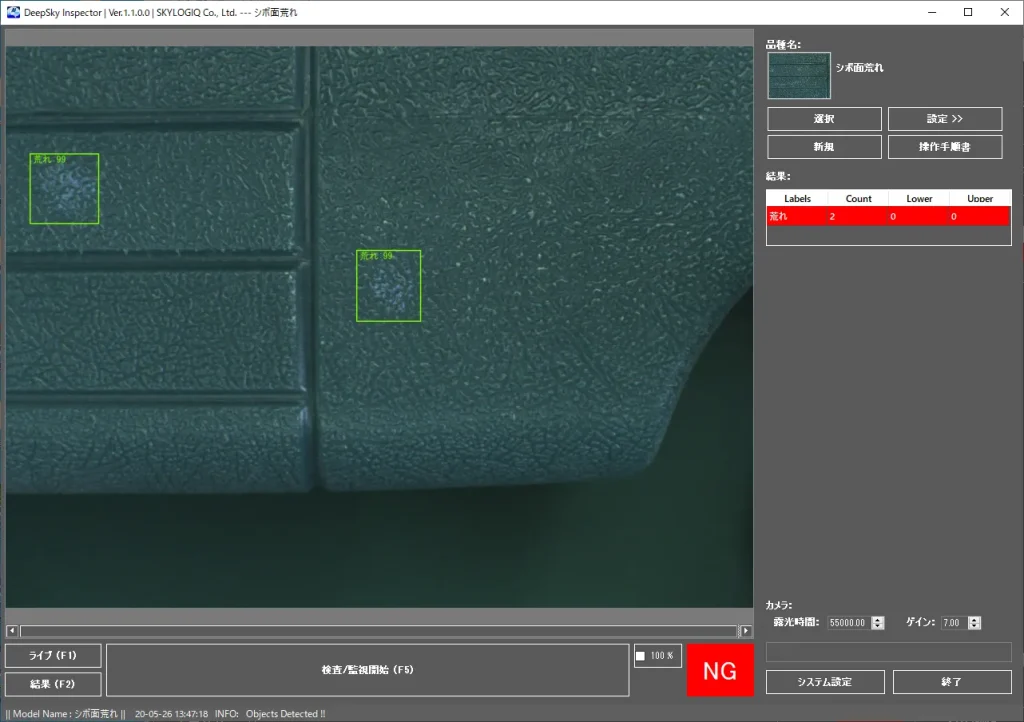
シボ面の軽微な荒れ2
不織布マスク上の加工ミス
不織布製品の欠陥検出は弊社で扱うことが多い課題です。ロール to ロールでの検査ではEasyInspectorを使うことが多いですが、柄入りの不織布やマスクなどに加工した製品上で欠陥を検出するのはDeepSkyが得意とするところです。加工後の製品は凹凸や重なりがあるため一般的な二値化処理では誤検出が多発してしまいますが、ディープラーニングでは欠陥の特徴学習して検出するため製品のばらつきにほとんど影響されません。
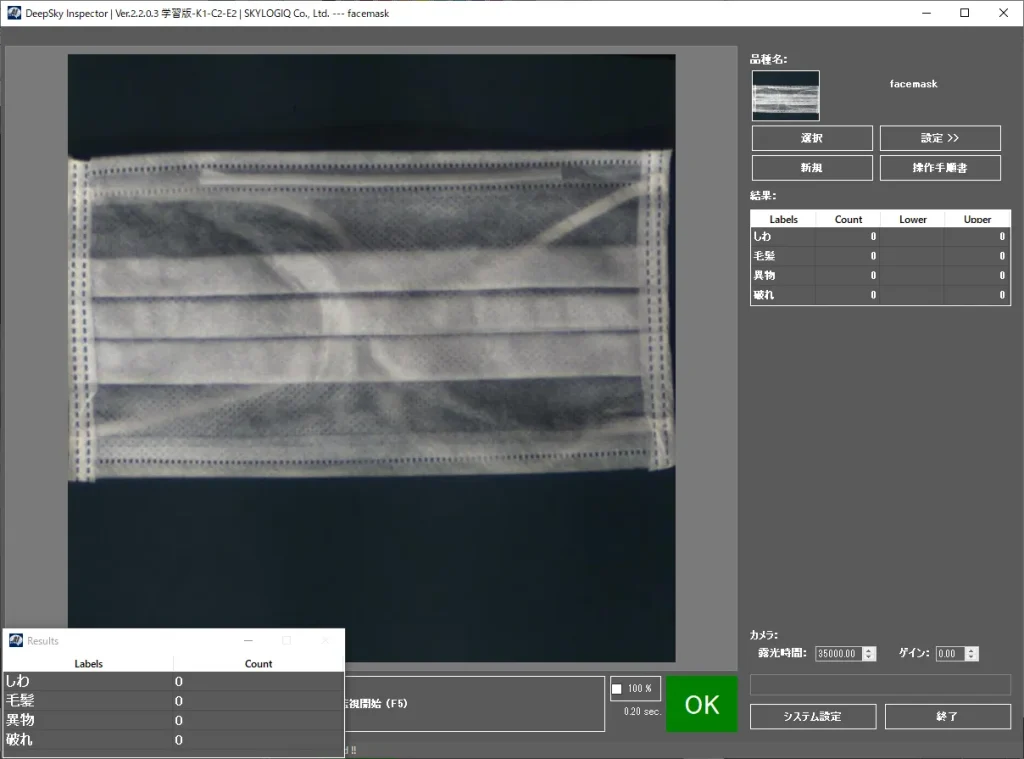
欠陥無しの状態(良品)
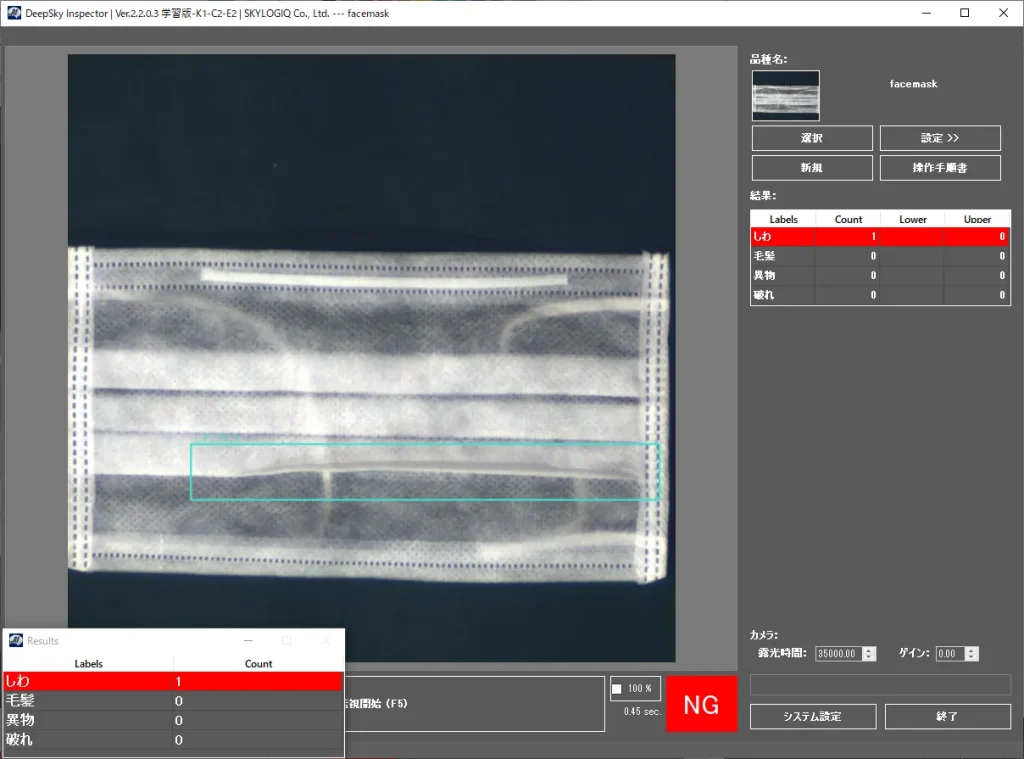
シワの検出
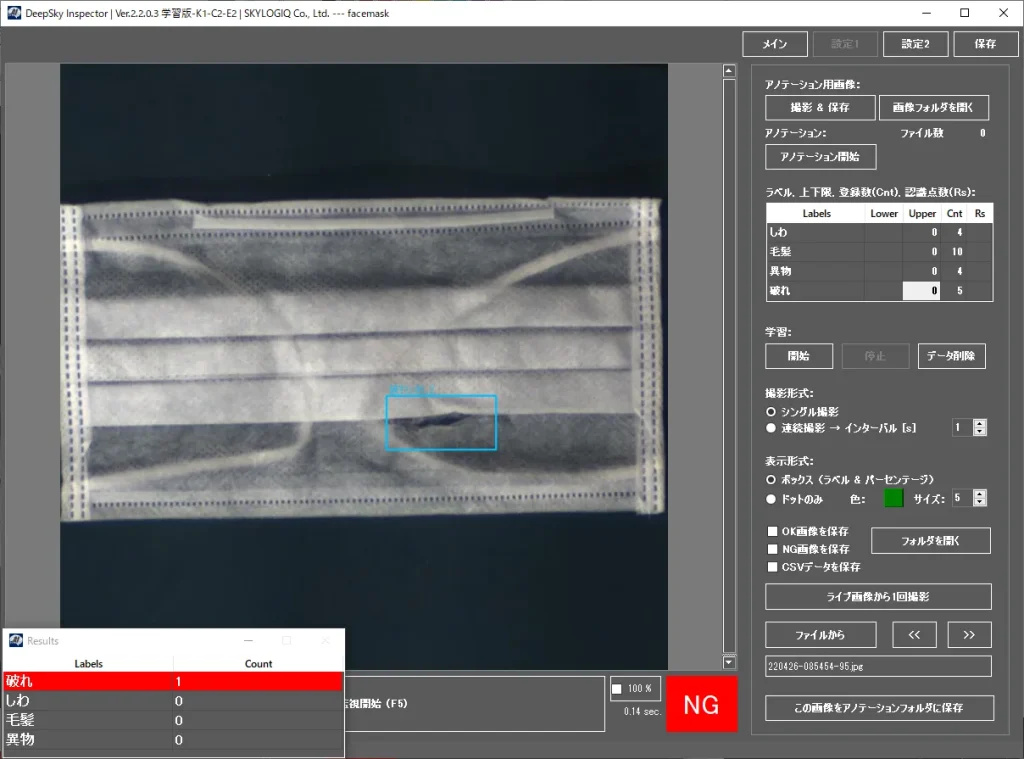
破れの検出
その他、異物も同時に学習させることで万が一異物が混入していた場合の検知も可能になります。
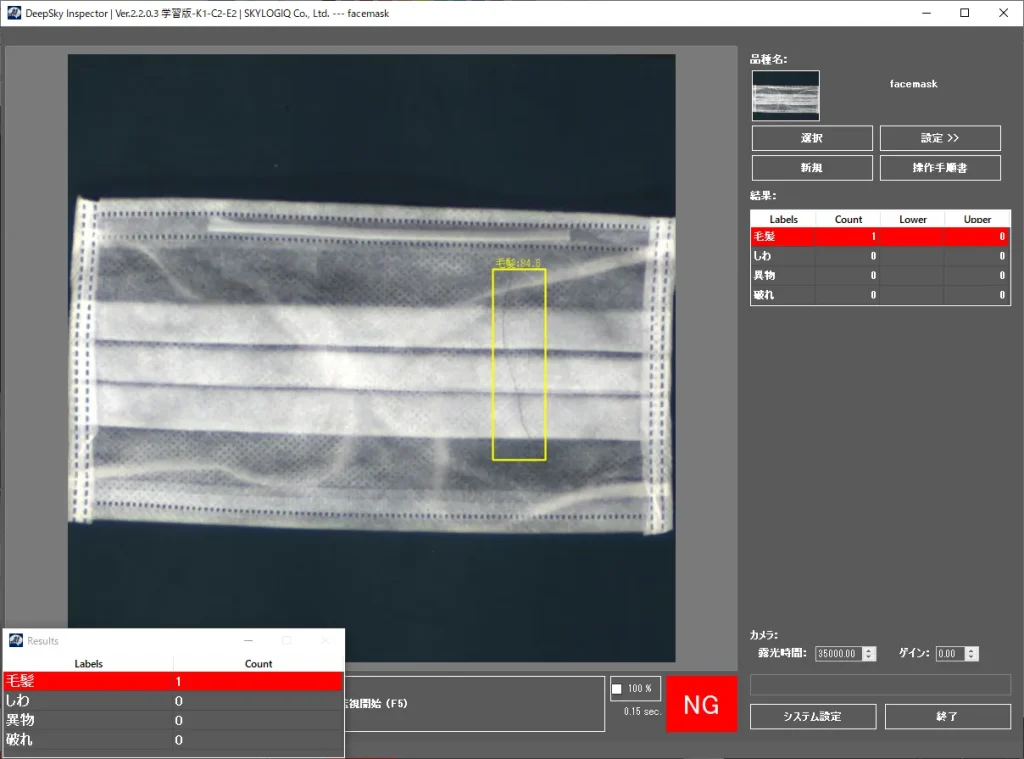
毛髪の検出
いもハンダの検出
いもハンダの形状と光沢を学習することにより、正常なハンダといもハンダの区別をしています。(画像クリックで拡大)
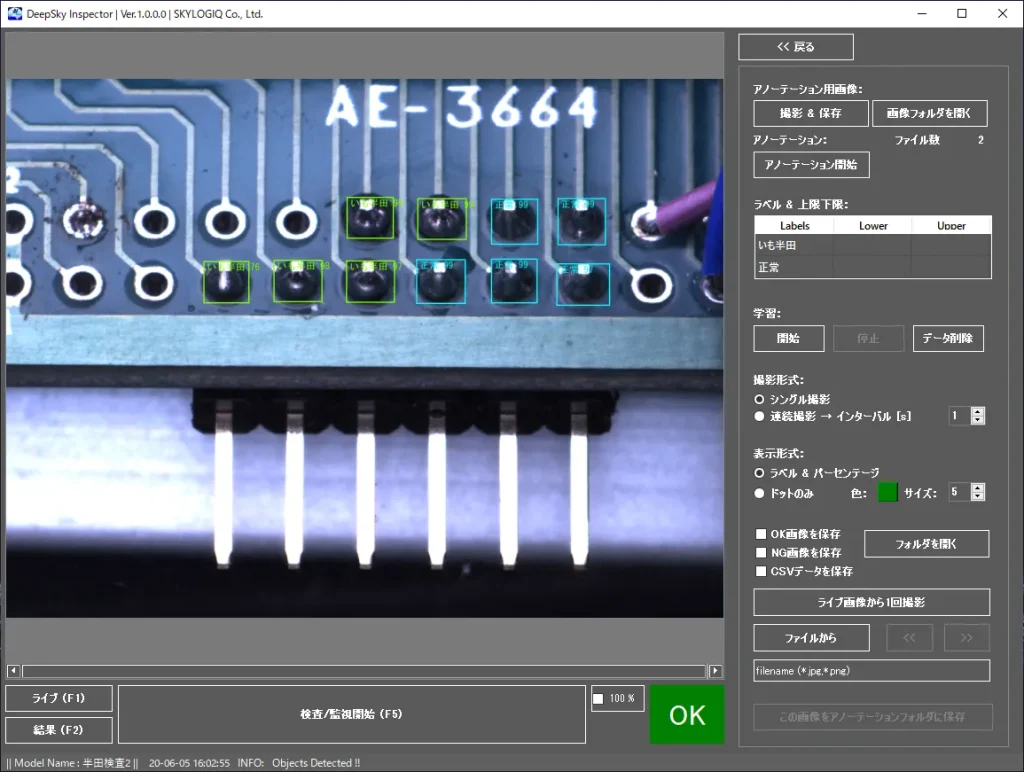
化粧ネジ加工ムラ
金属製品はギラつきがあり、照明や姿勢の若干の違いにより見え方が変わるため誤判定が多い検査対象の一つです。特に転がりやすい形状のもの(円筒など)は姿勢の制御が困難です。この例では円筒状の金属の加工ムラを、ランダムな姿勢の状態で検出しています。
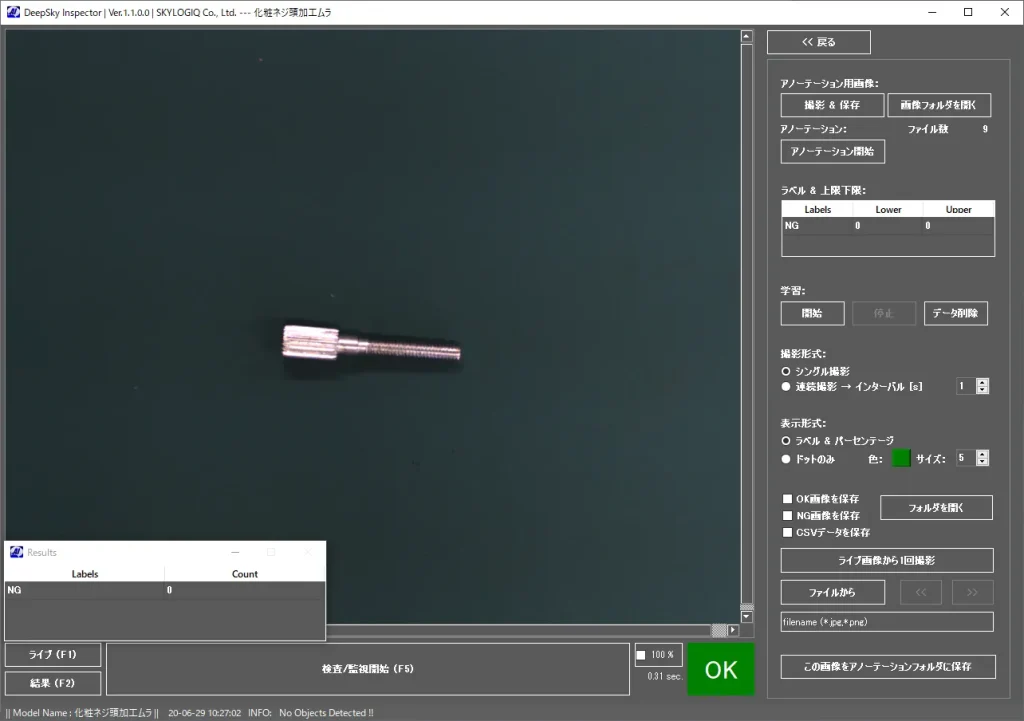
OKの状態では化粧ネジの頭の部分が均一に加工されています。
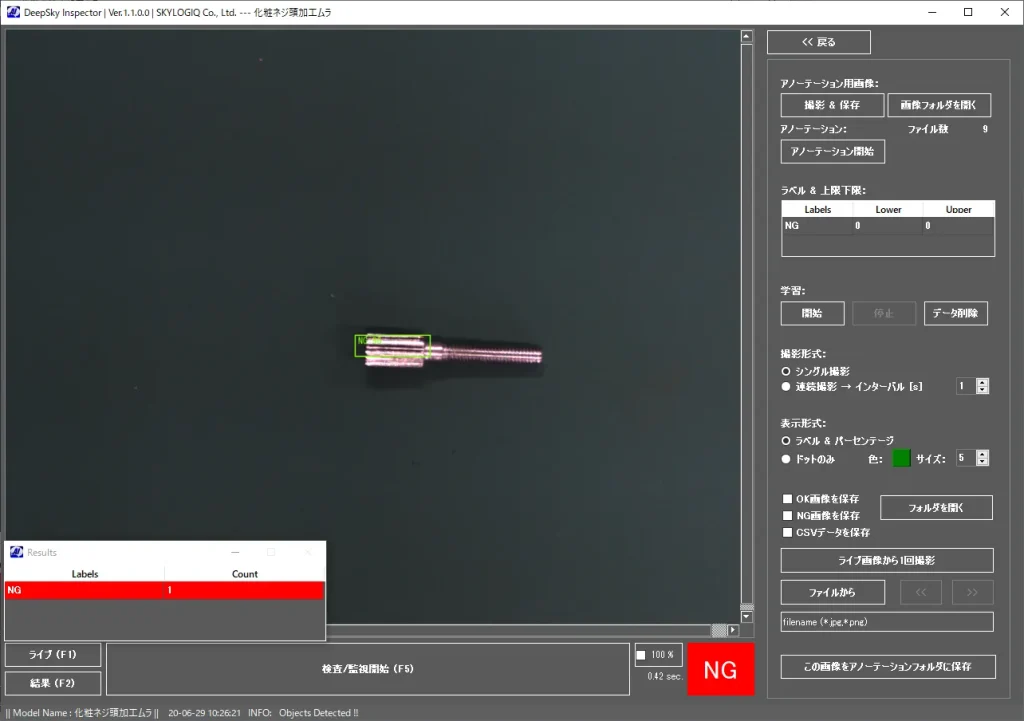
NG品では一部の加工に不均一な部分が見られます。
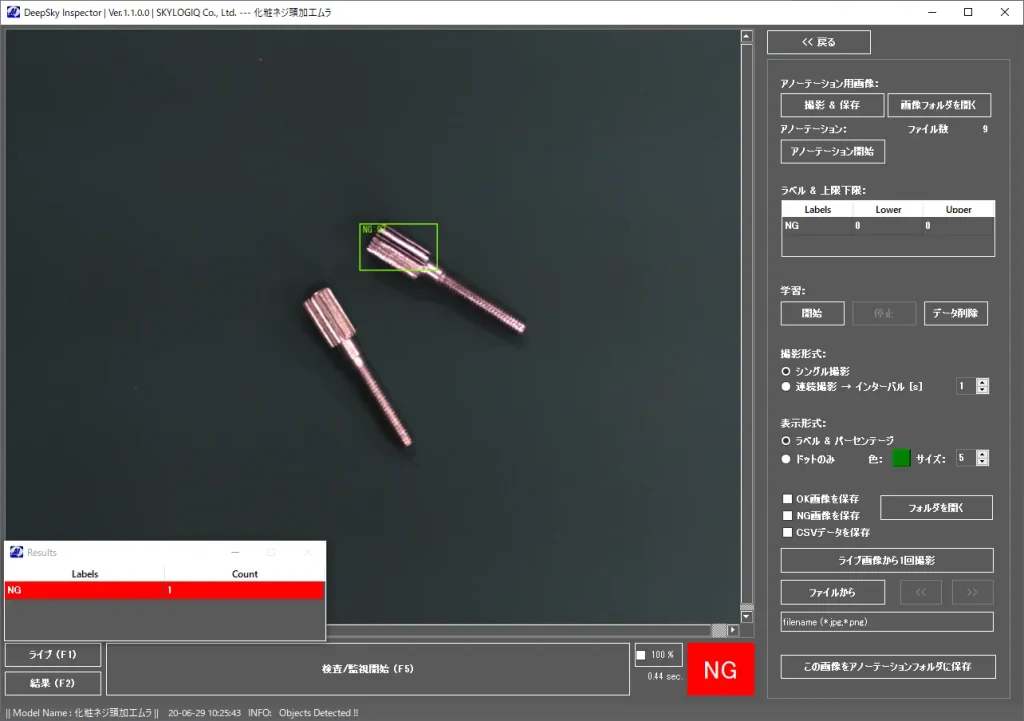
複数のOK/NGを並べた状態でもNGのみ検出できます。
ソケットピン曲りの検査
端子のピン曲りを確認しています。部品の姿勢や数に関わらず、コンベア上で曲がったピンを検出しています。
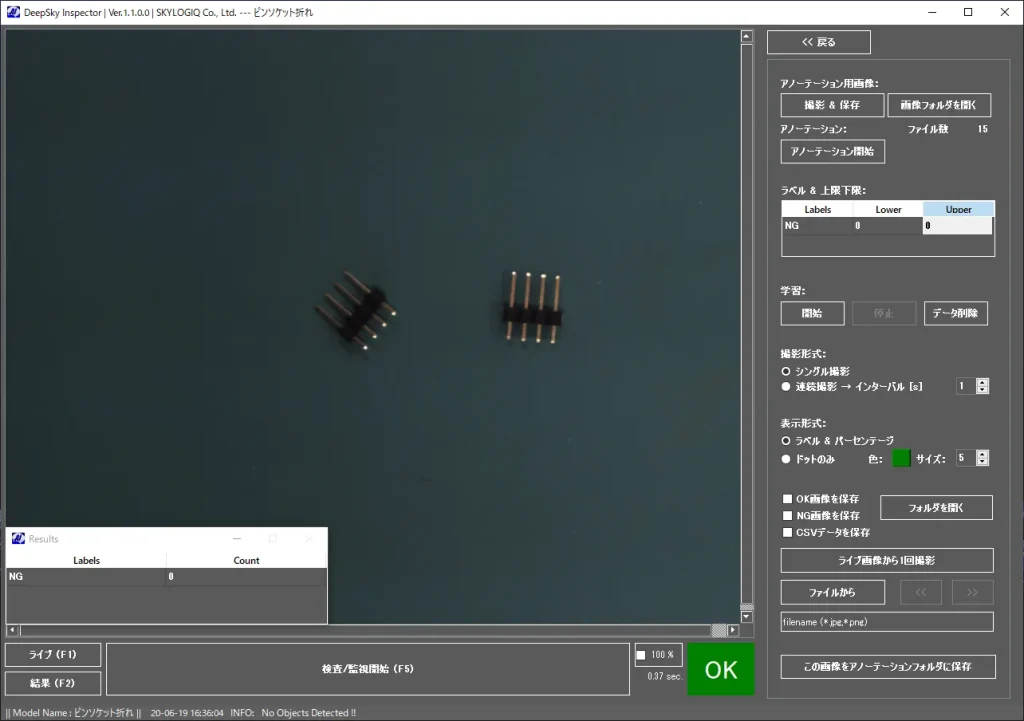
曲がったピンがない状態(OK)
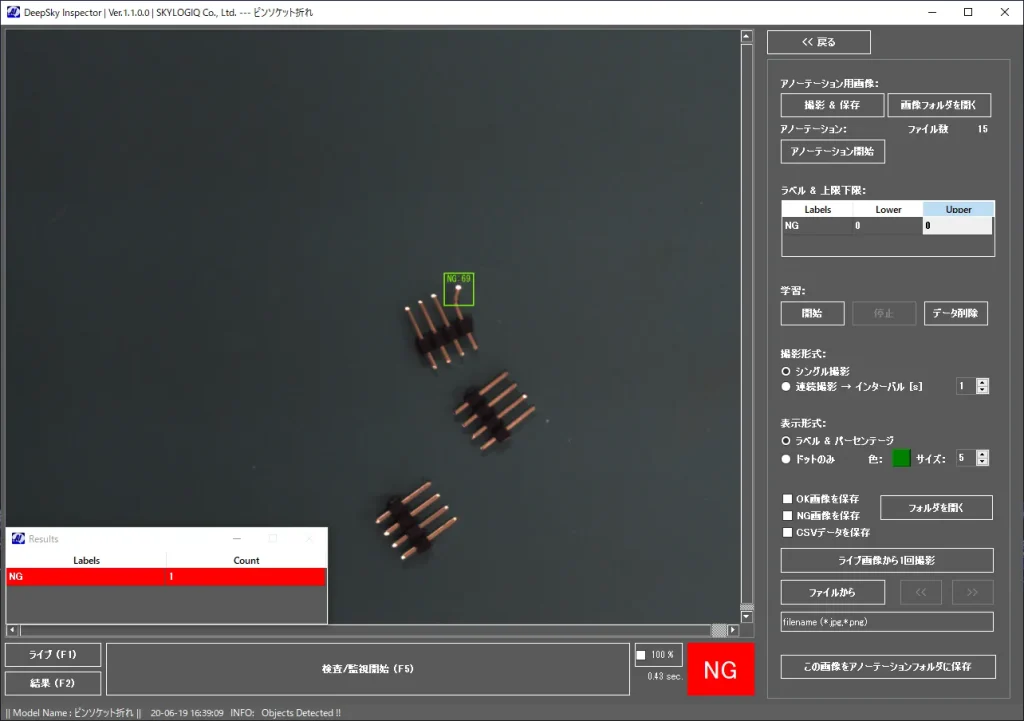
曲がったピンを含んだ部品が撮影された時(NG)
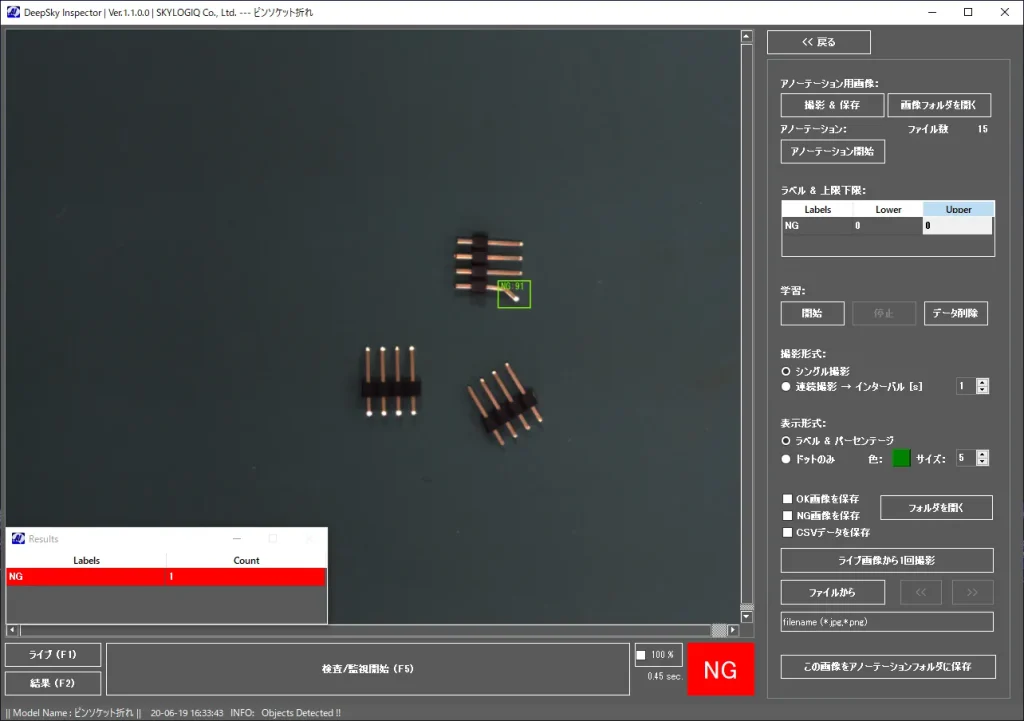
金属の打痕(ダコン)
金属製品の欠陥で最も多いものの一つにダコンが挙げられます。金属の傷や打痕は金属表面のギラつきや照明の角度などの条件によって見つけにくい部類に入りますが、コンベア上を流れる部品を連続で複数回検査することでより発見しやすくなります。この例は比較的大きなダコンです。
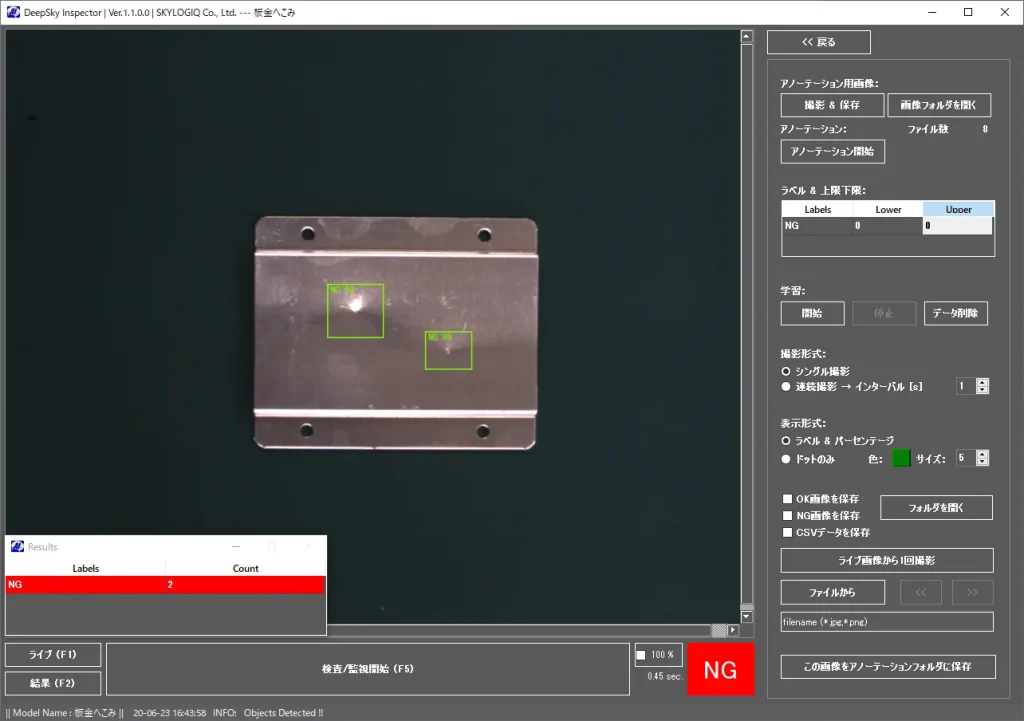
大小2つの打痕があります。上下の線状の反射は無視しています。
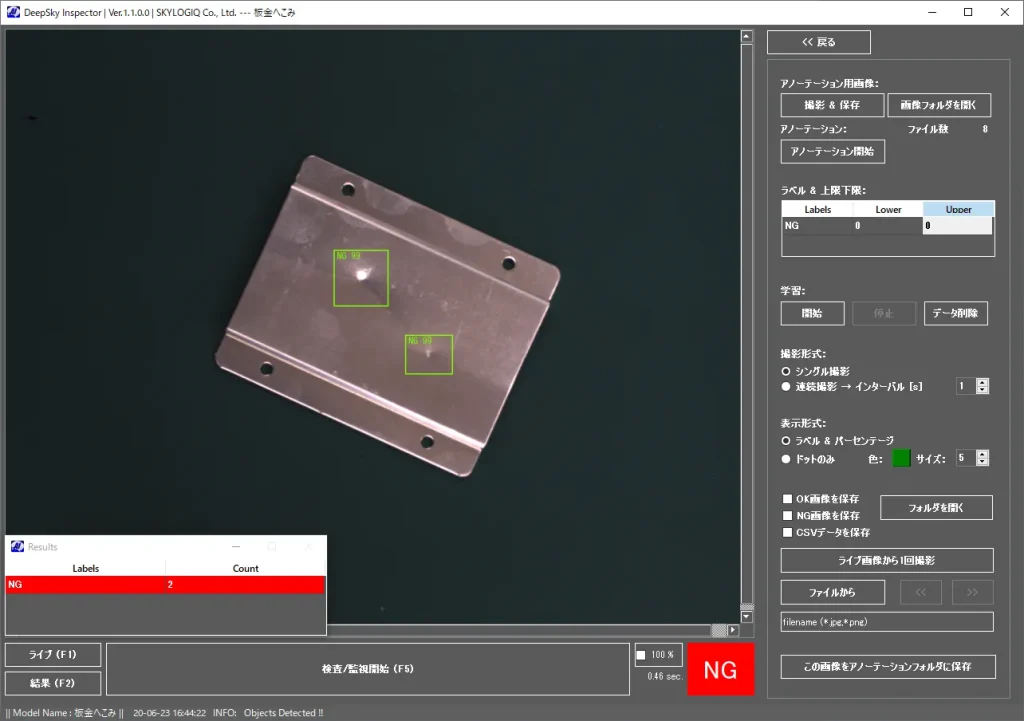
製品の姿勢によらず検出可能です。

ギラつきがある場合でも、学習により打痕の検出が可能になります。
棒の折れと黒点の検出
棒の折れと黒点を検出する設定です。
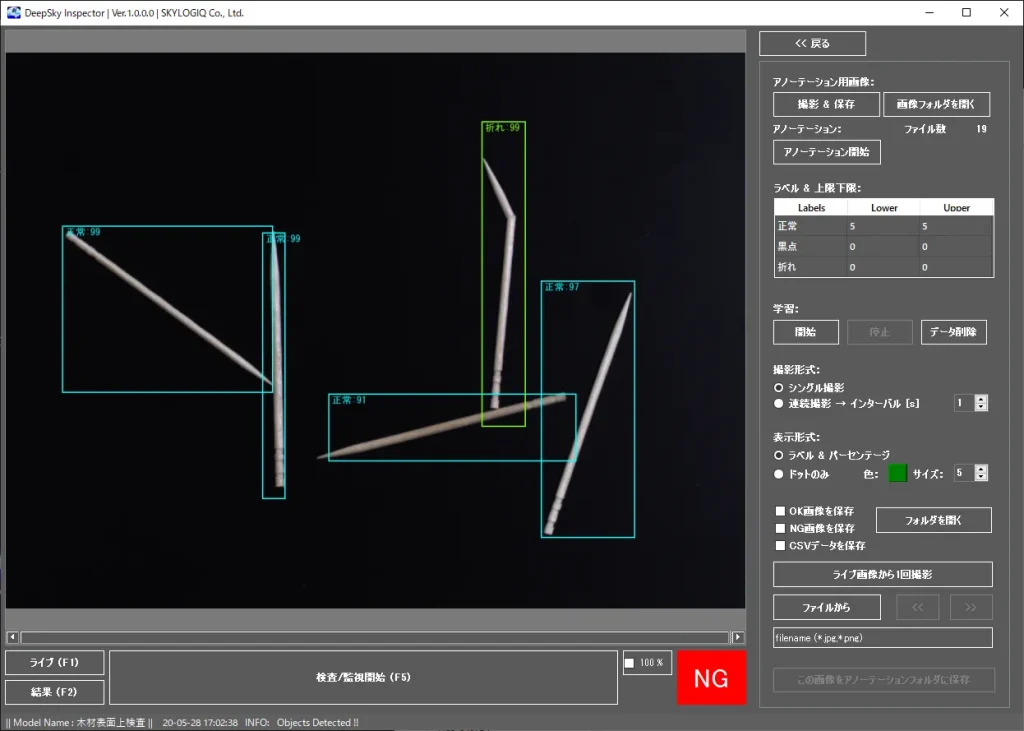
棒の折れを検出しています。
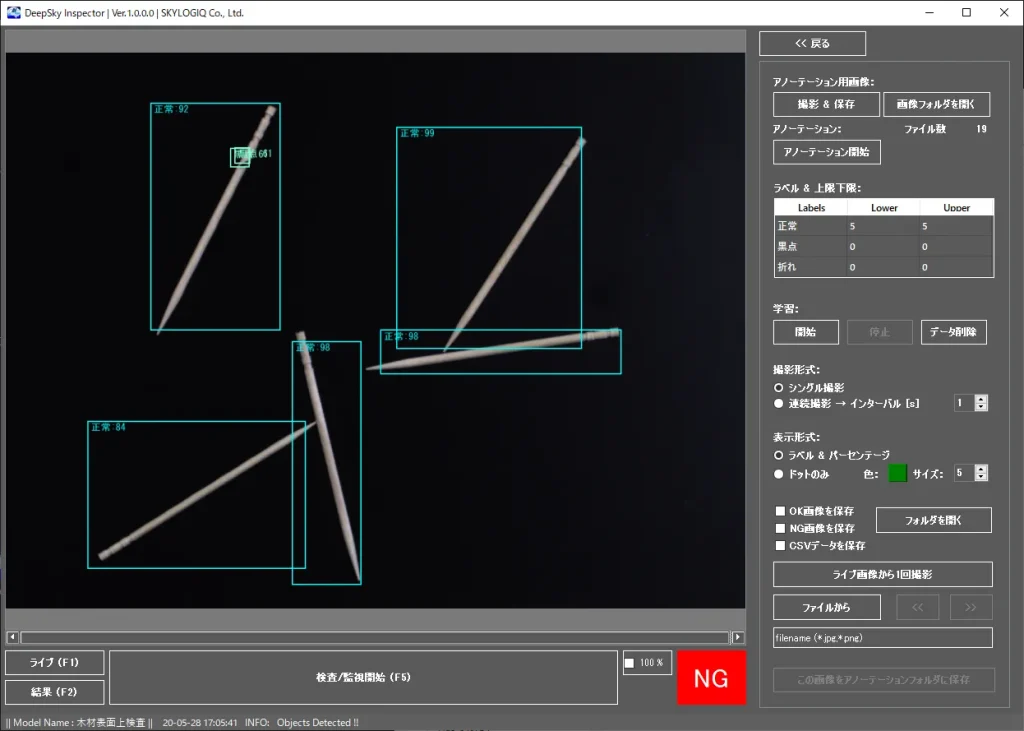
左上の棒の黒点を検出しています。
プレス品の形状不良
プレス品の形状の不良を検出しています。この例では角度が正しくない物を検出しています。
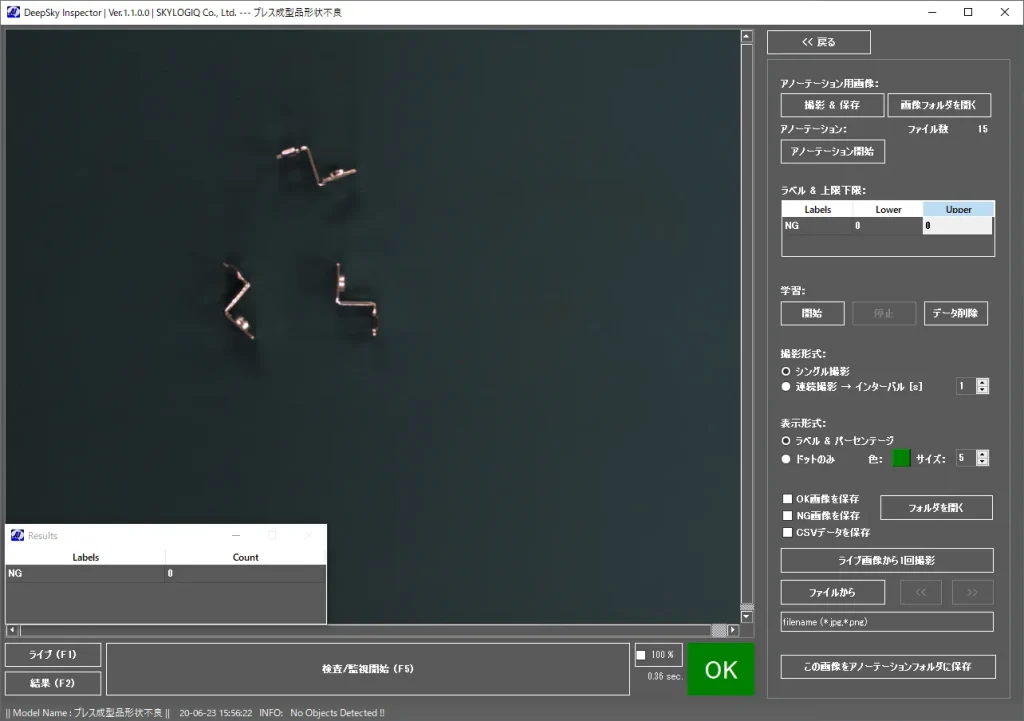
正しい部品のみの状態(OK)
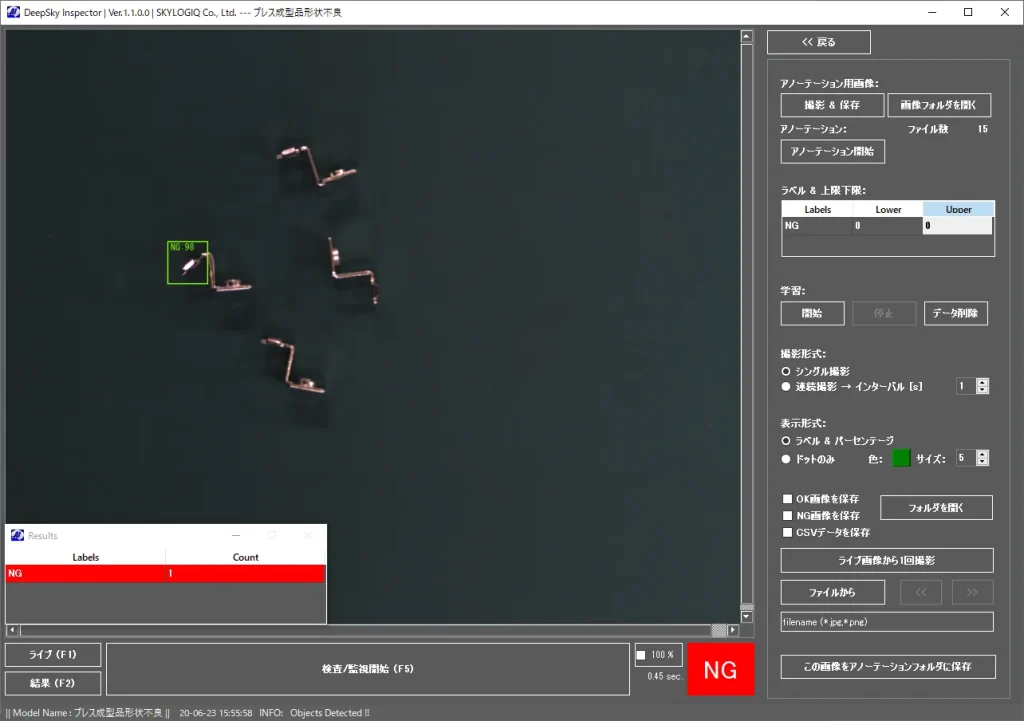
部品の角度が正しくないものが含まれている状態(NG)
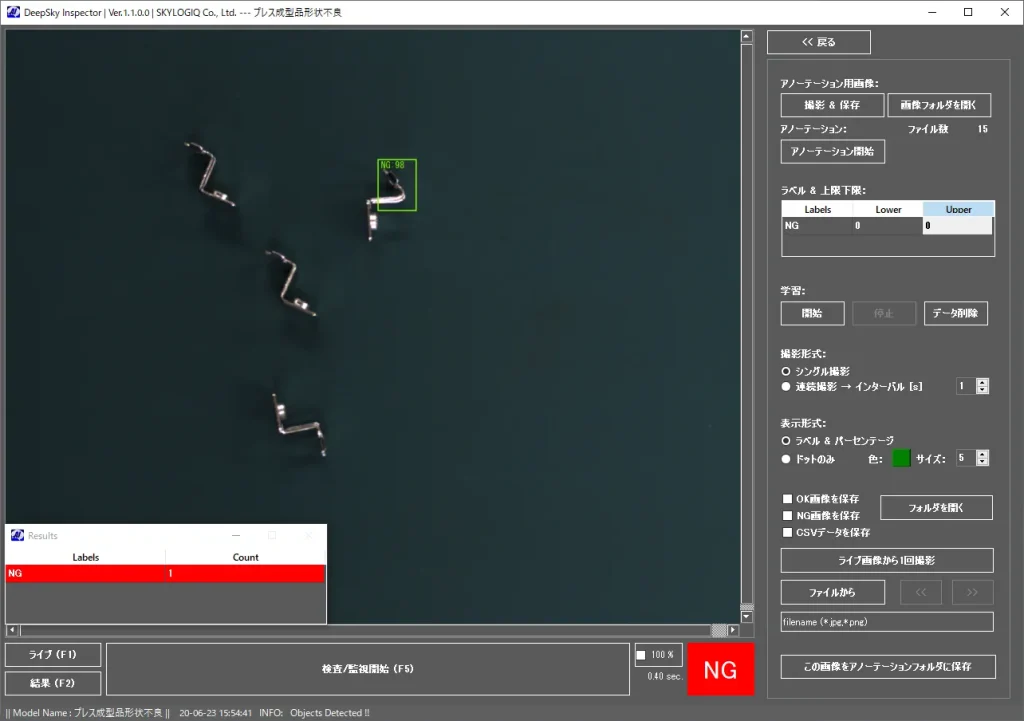
ペットボトルラベルの破れ検査
ペットボトルラベルに生じた小さな破れを検出しています。
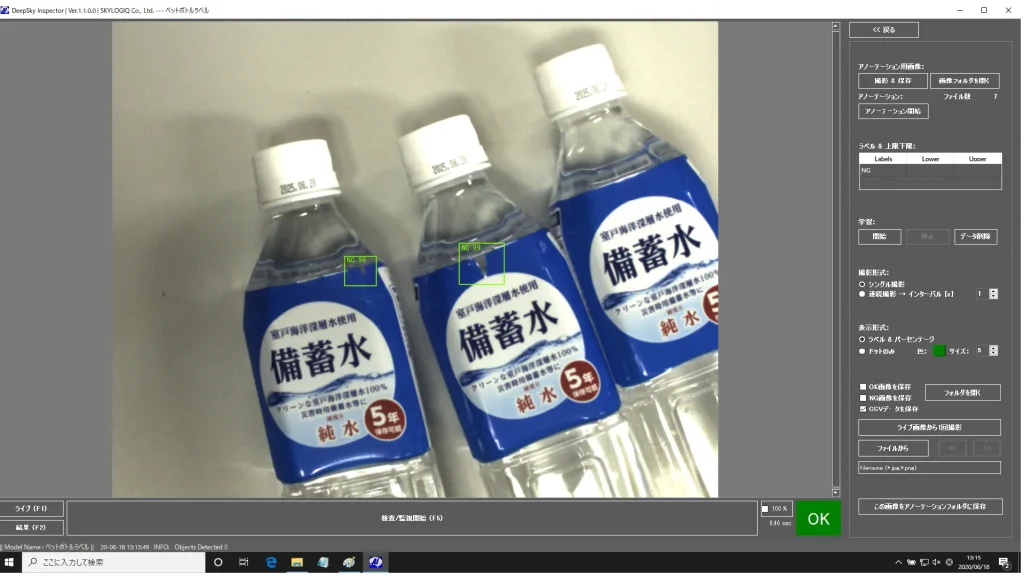
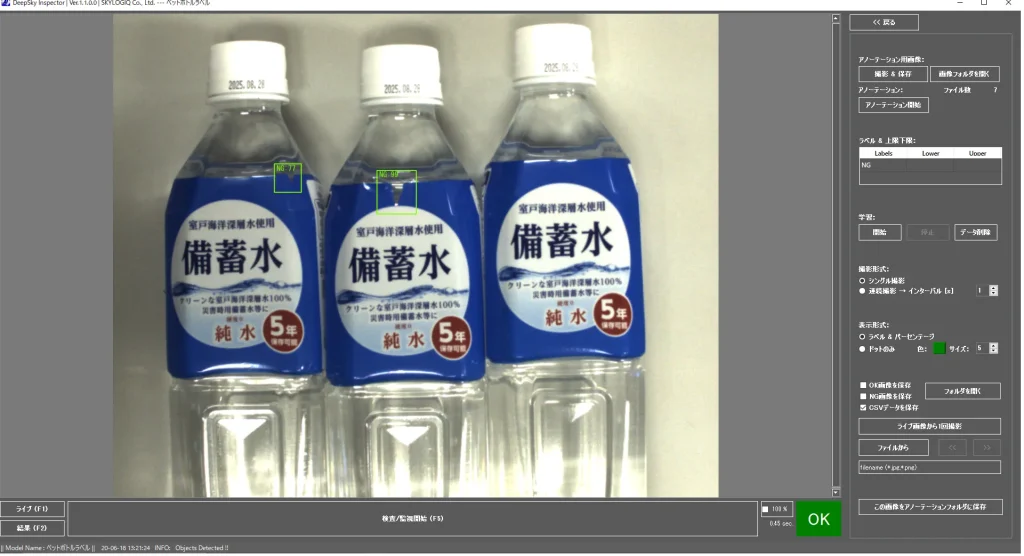
金属加工品の変色
サビの発生、メッキむらなど、金属部品に発生する変色を検出します。
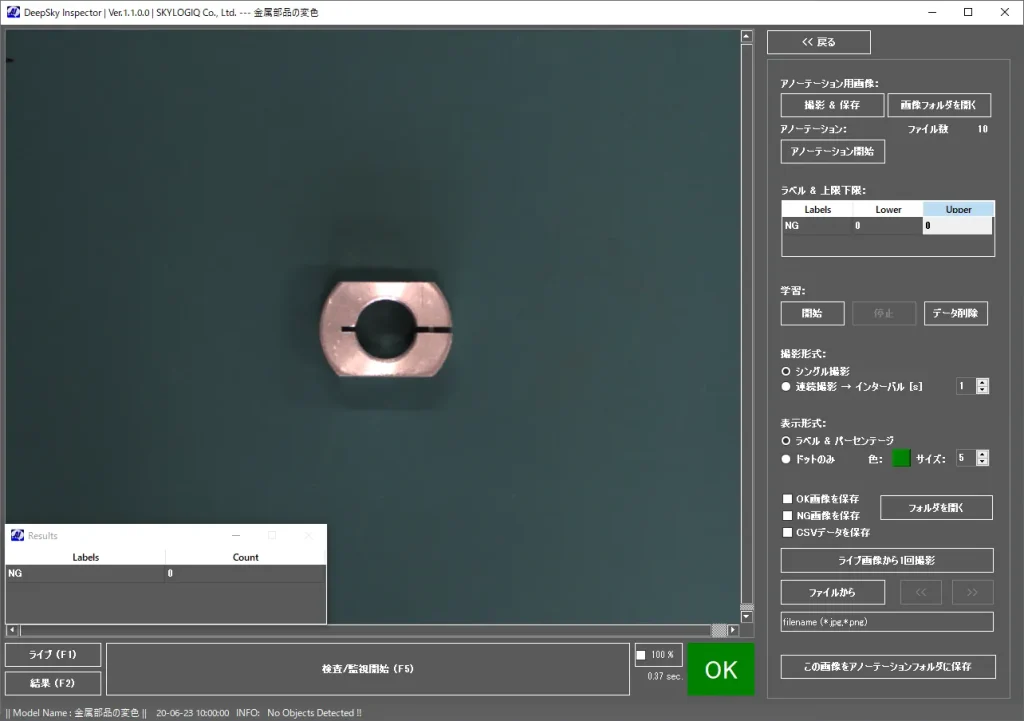
正常な状態(OK)

一つの部品の左上に黒ずみが発生しています。
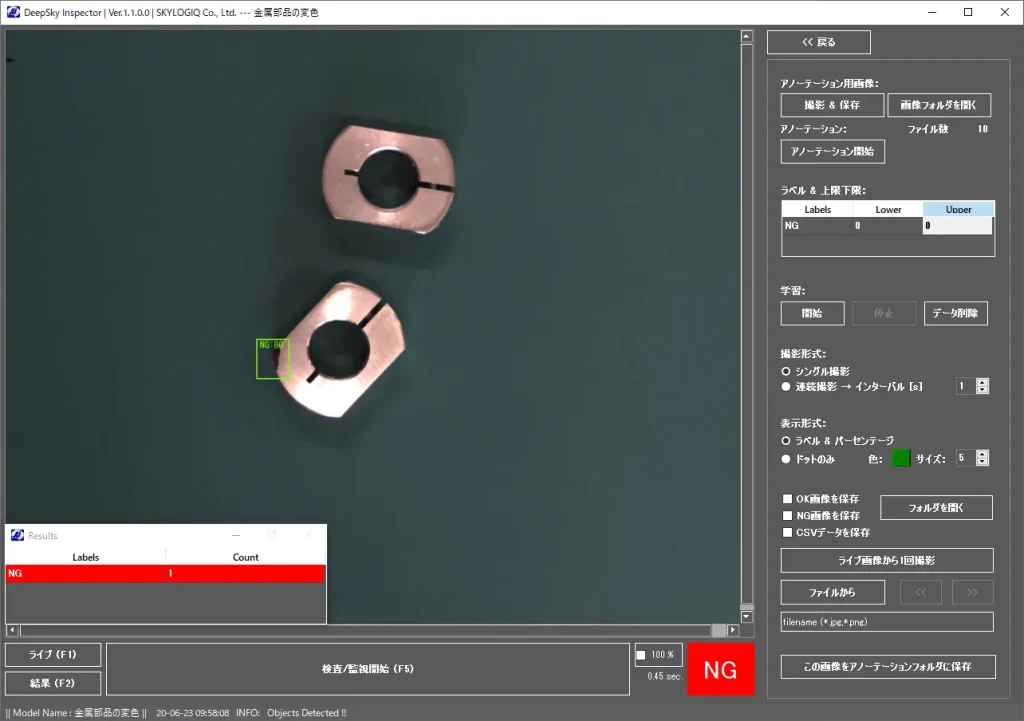
金属特有のギラつきに左右されにくい検出です。
コネクタピン曲り検査
コネクタのピン曲りをコンベア上で検査している例です。
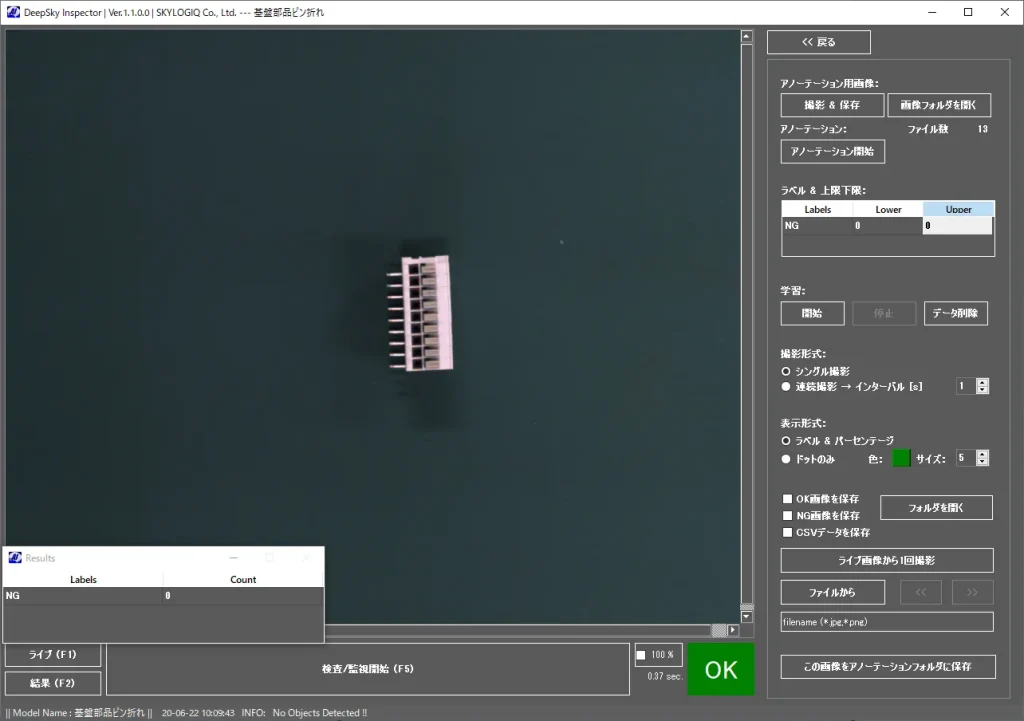
正常な状態(OK)
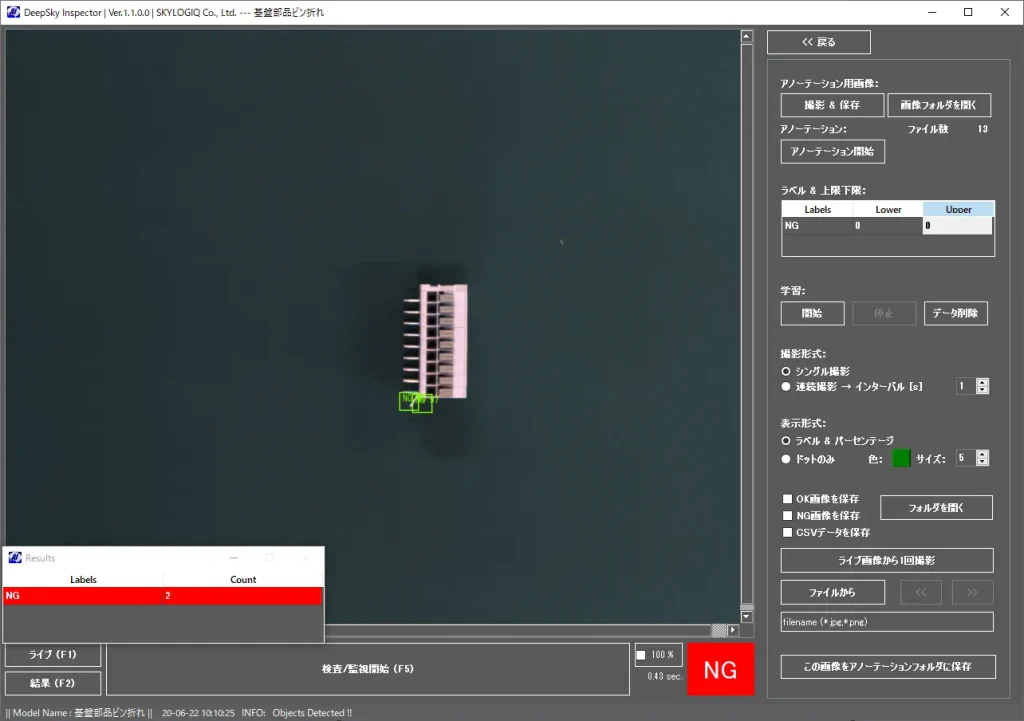
ピン曲りが発生した状態(NG)
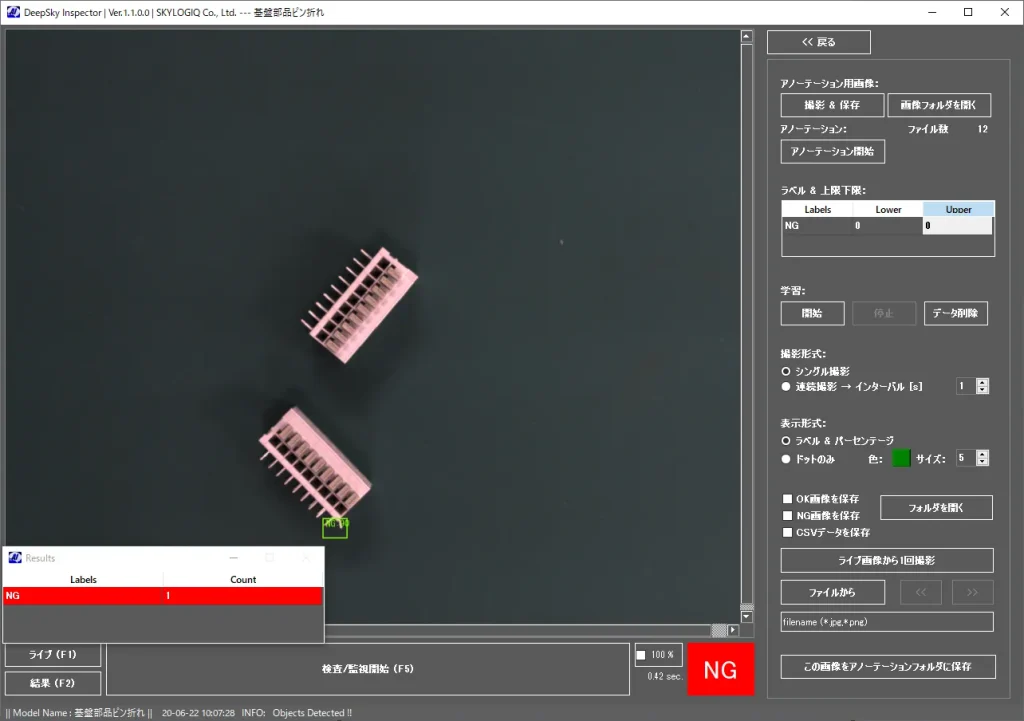
コネクタの位置や姿勢、数に関わらず曲りを検出しています。
穴加工のひげ検査
ドリル加工やプレス加工の穴に生じるヒゲやカスを検出します。同様にドリルカスによる製品の傷(穴付近に同心円状に発生するもの)も検出可能です。
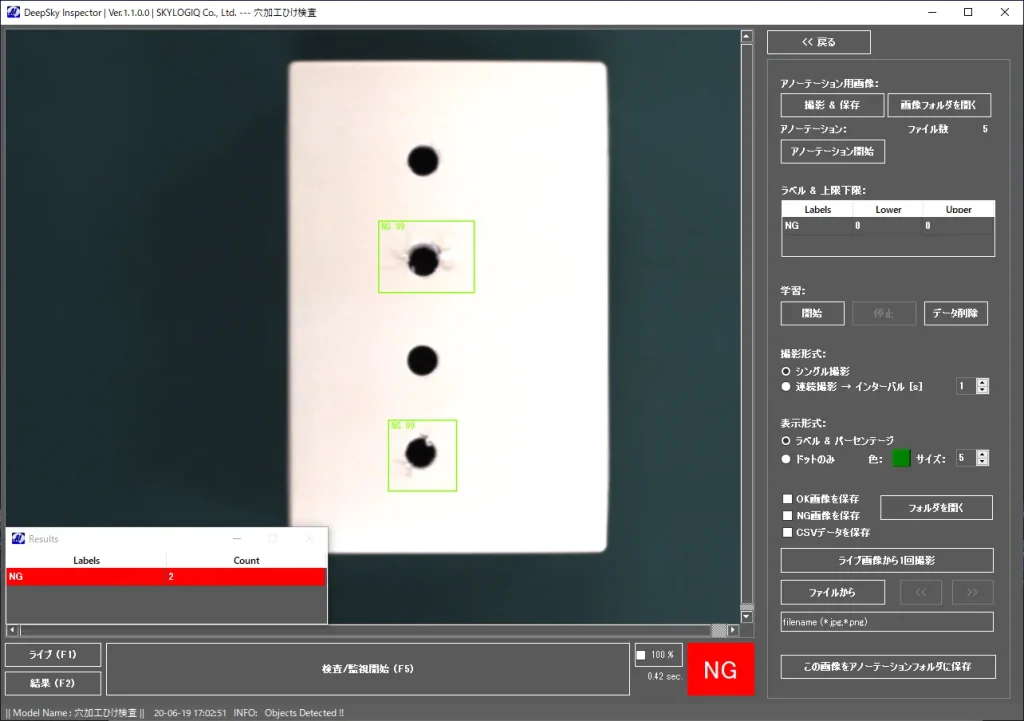
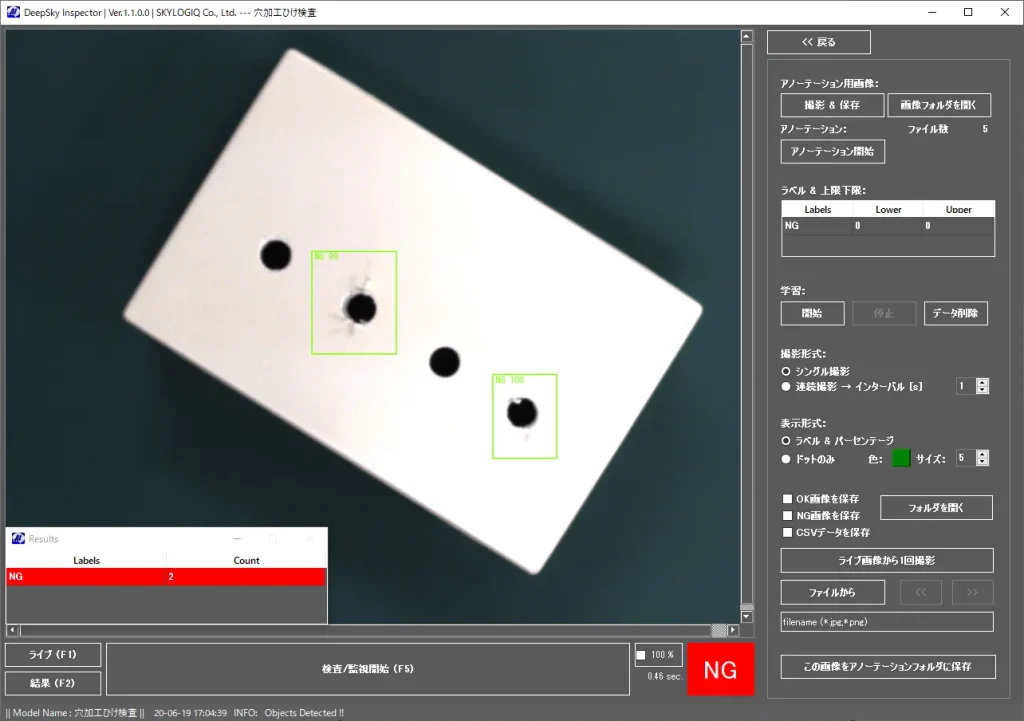
成型品のバリ
プラ成型品のバリを検出している例です。同様にショートや黒ブツなどの検出も同時に行うことができます。
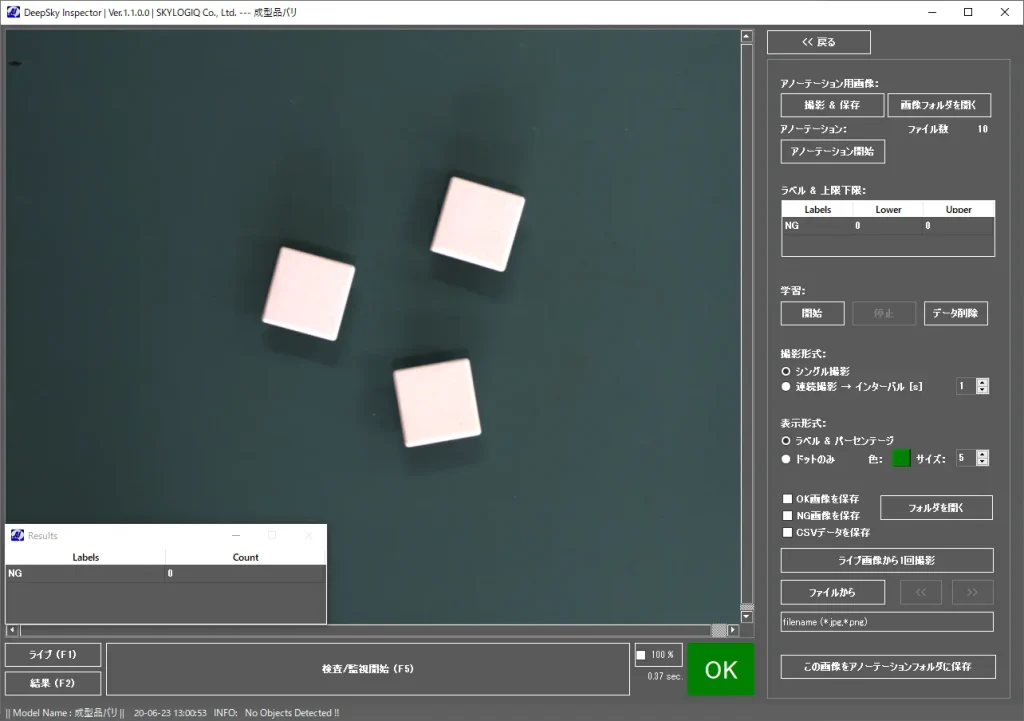
バリのない状態(OK)
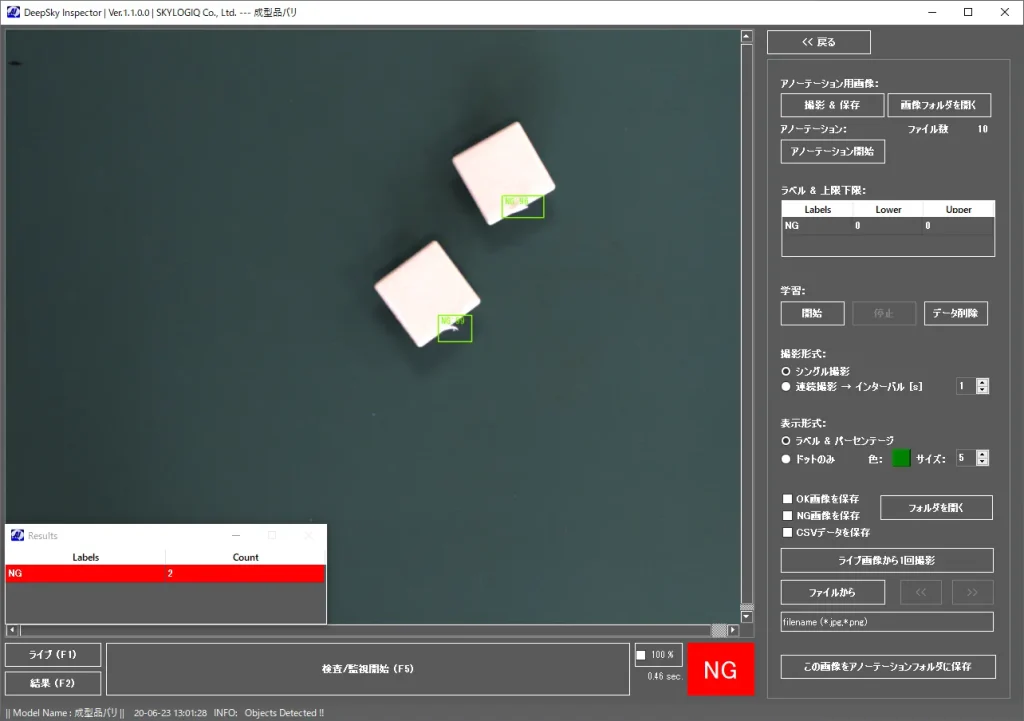
バリのある部品(NG)
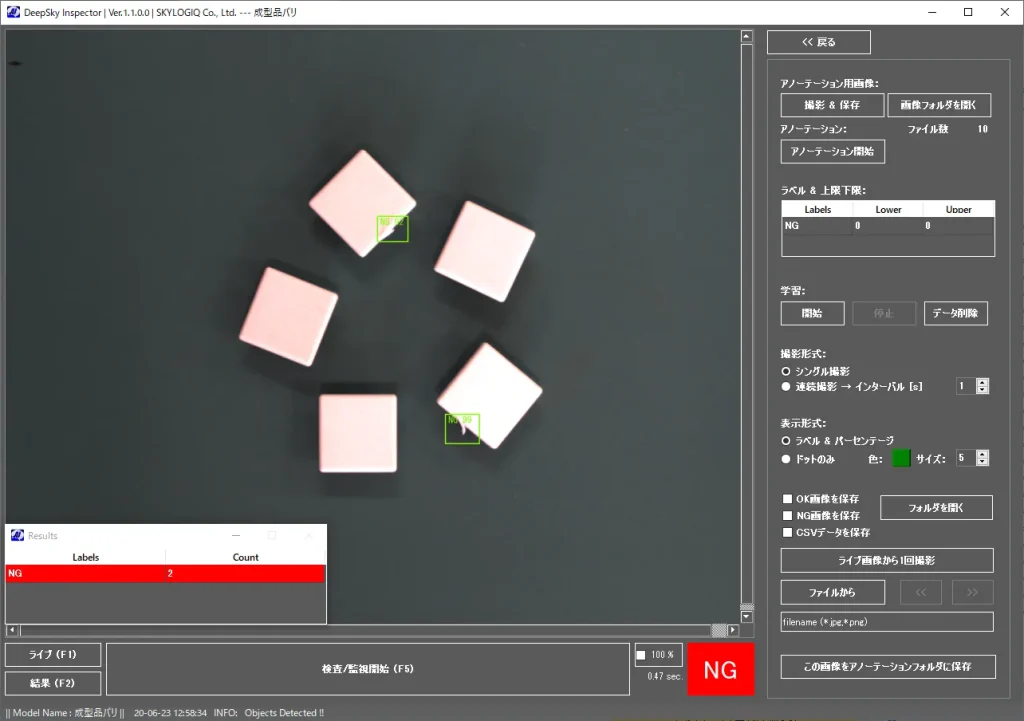
合格品と不合格品が混在した状態(NG)
シール剤や接着剤のはみ出し検査
接着剤やシール剤を自動塗布機によって塗布する過程では塗布の過少によって「切れ」が、過多によって「はみ出し」が発生することがあります。この例では接着剤を塗布して部品どうしを嵌合した時に発生する接着剤のはみ出しを検出しています。
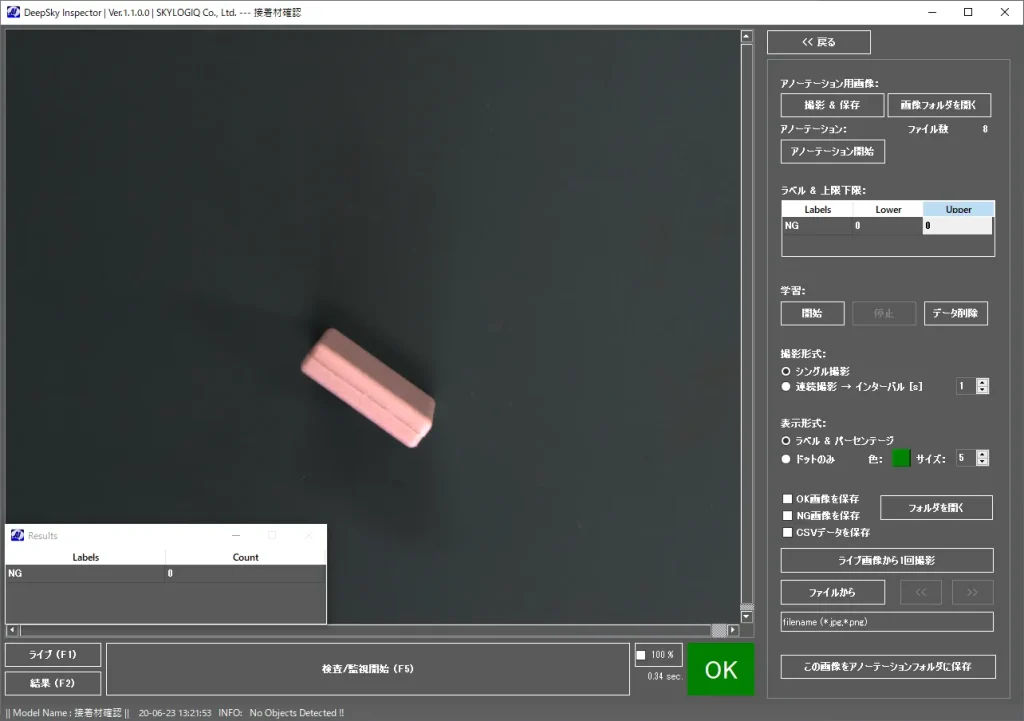
正常な状態(OK)
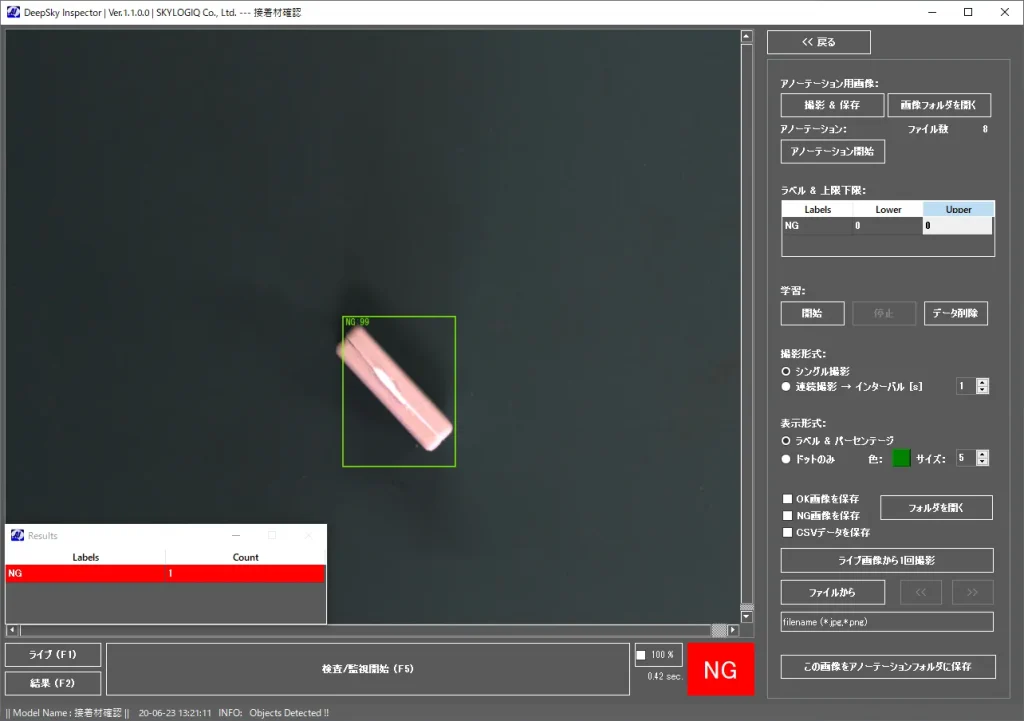
はみ出しが発生した状態
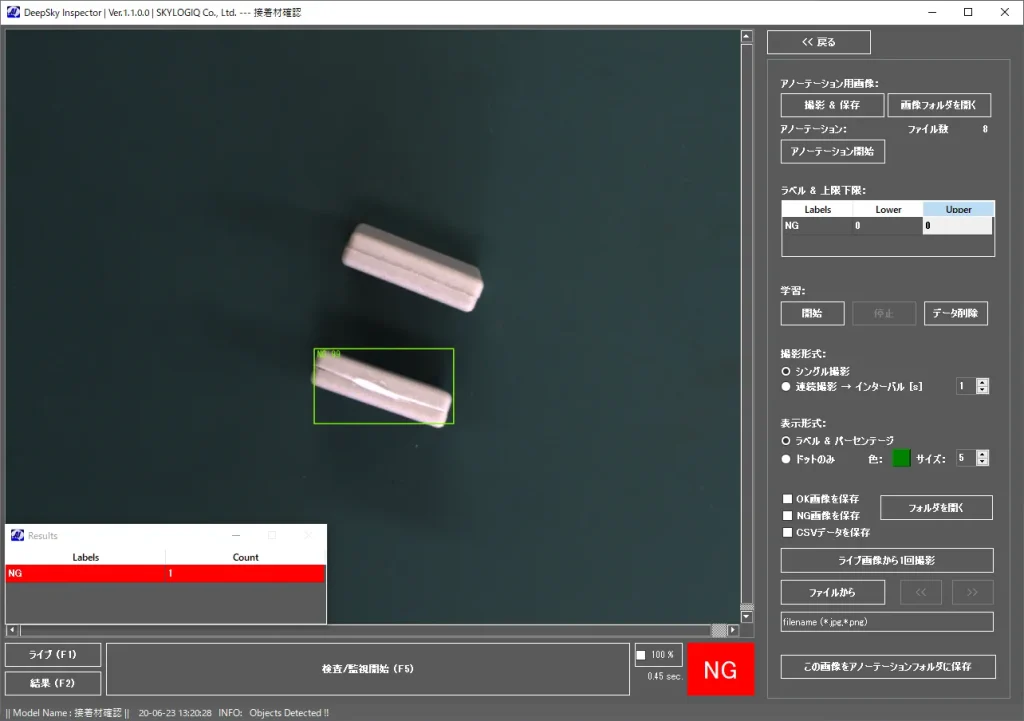
2個以上の同時検査も可能です。姿勢や位置に関わらず検出できます。
電子部品足曲りの検査
コンベアで搬送される電子部品の足曲がりを検出しています。
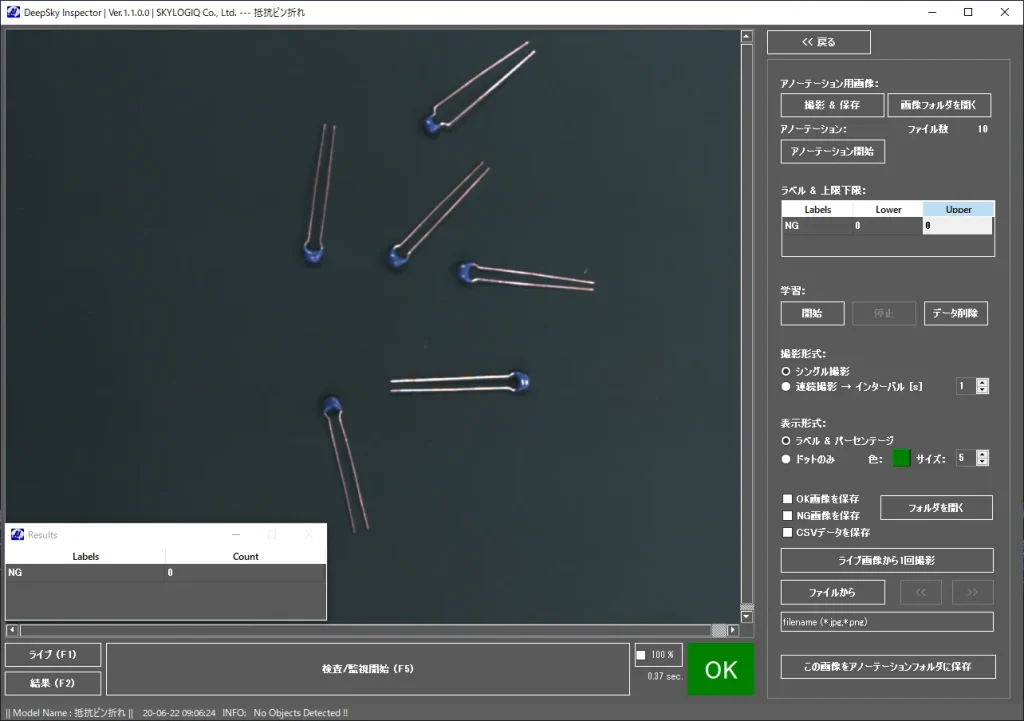
足曲がり部品がない状態(OK)
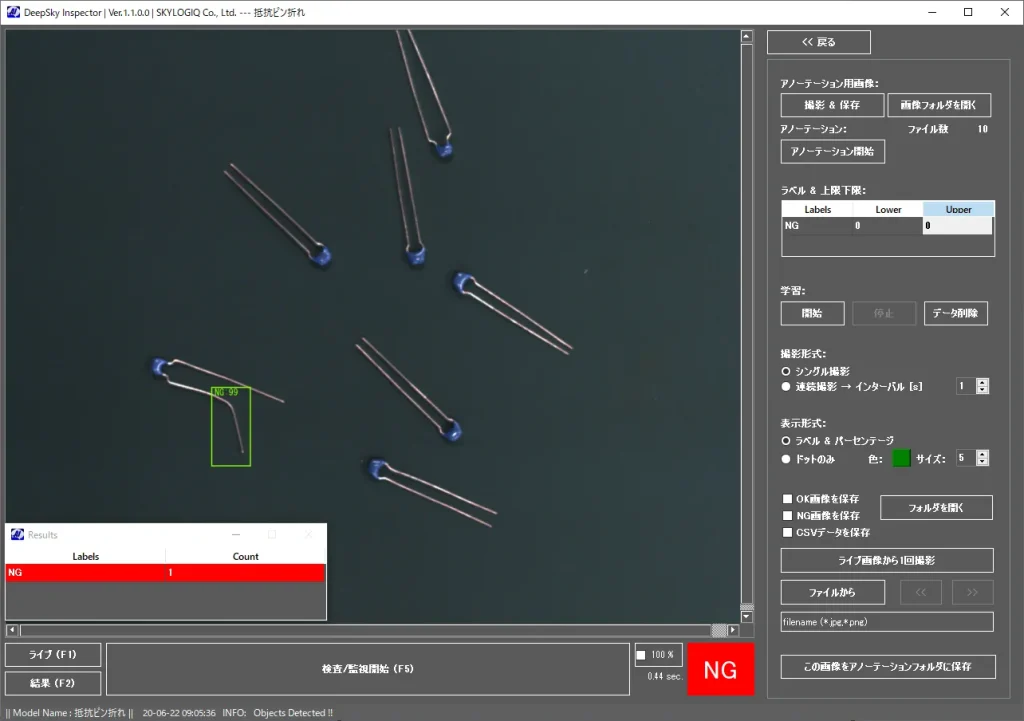
足曲がり部品がある状態(NG)
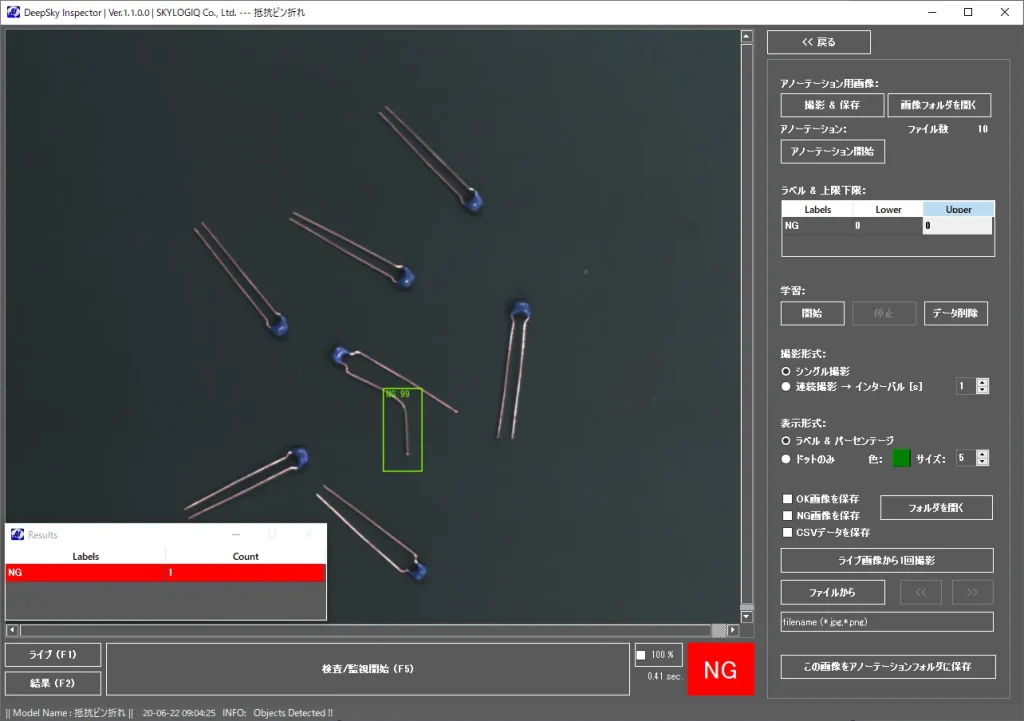
成型品ショートショット
プラスチック成型品は端部でショートが発生しやすく、一旦コンベア上に落とされるとランダムな姿勢になるため検査が困難になる傾向があります。この例ではコンベア上にランダムな姿勢で流れてくる製品を定点で検査し、NG(ショートショット)を検出することを想定した例です。
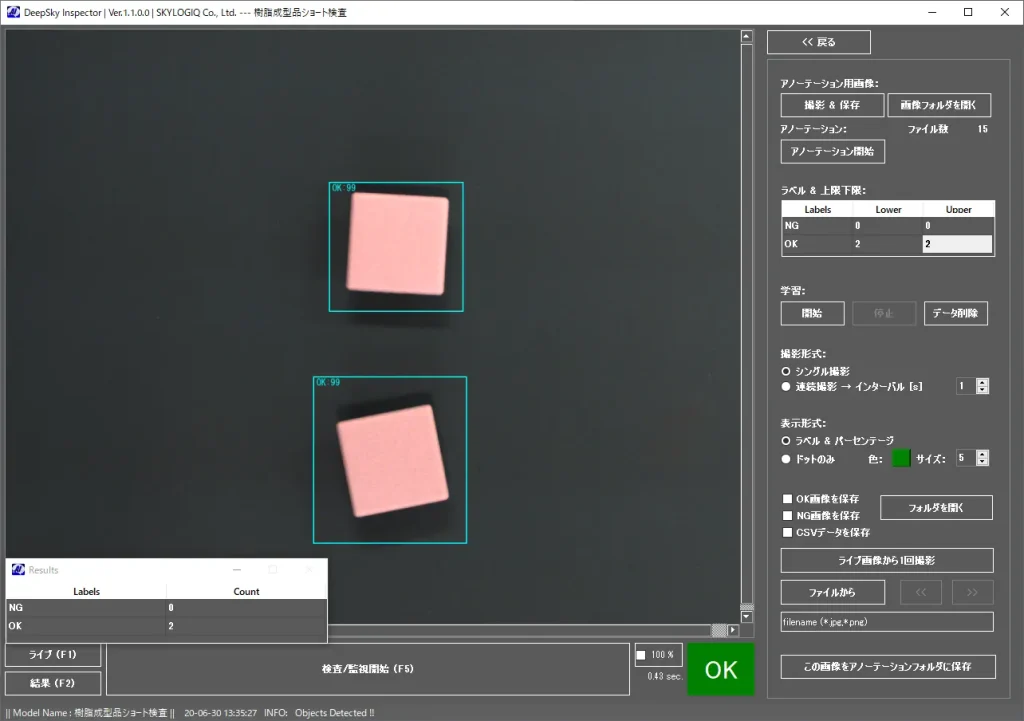
OKの状態(ショートなし)
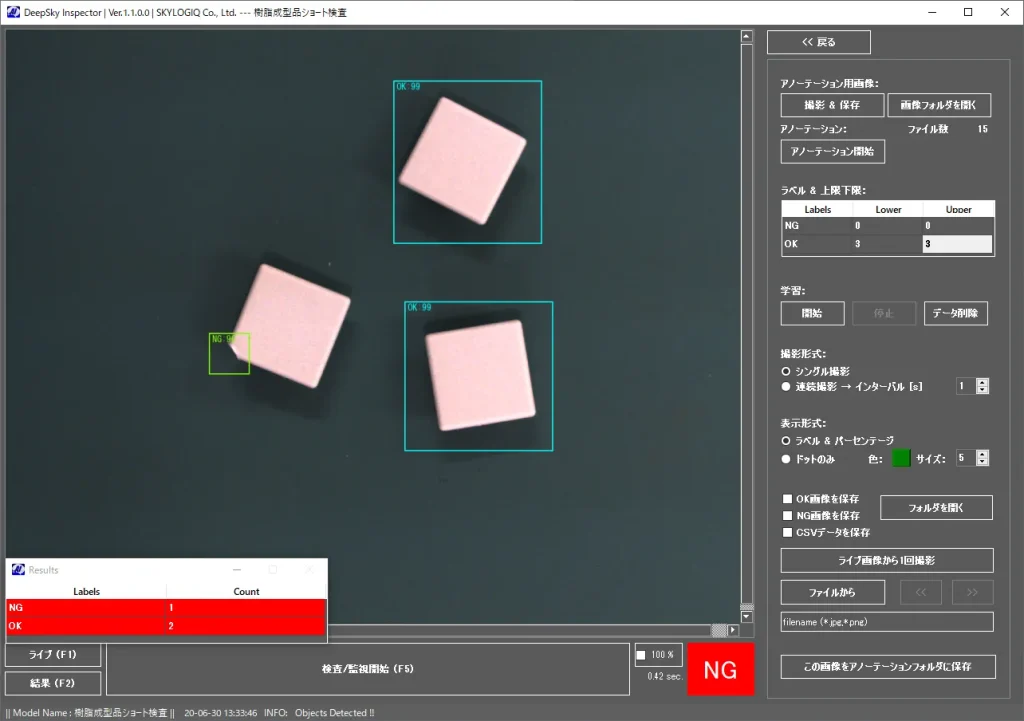
画角内の製品にNGが含まれている例
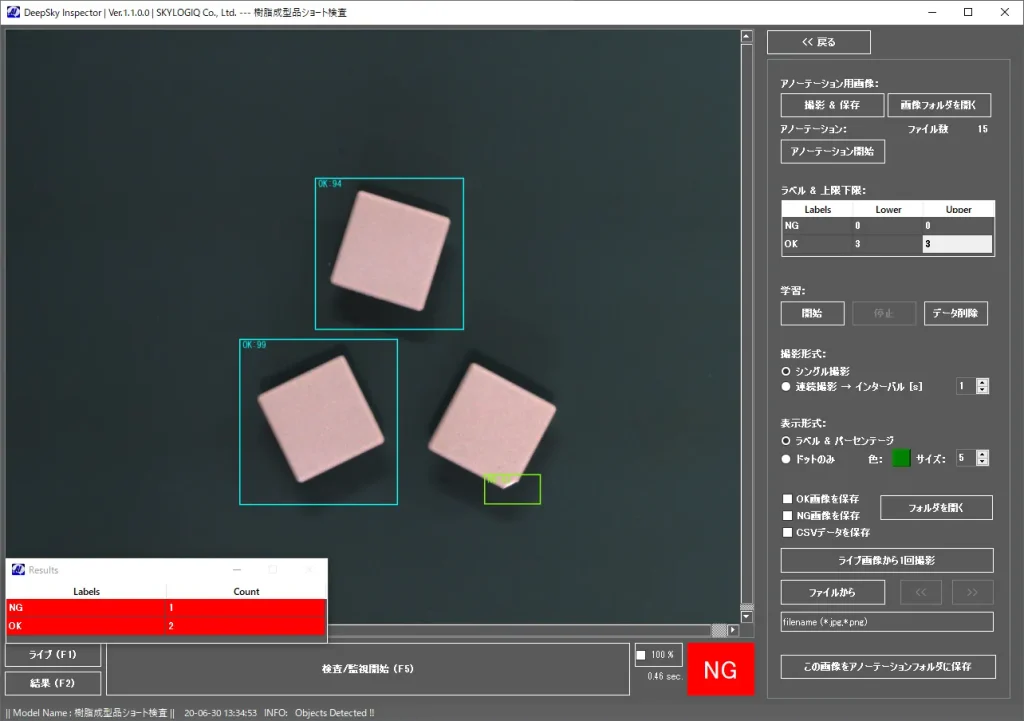